Table of Contents
A fiber laser cutting machine is a device that uses a fiber laser as a light source and uses a laser beam to cut materials with high precision. When using a fiber laser cutting machine, you need to follow the following steps to ensure that the equipment operates safely and efficiently. The following is a fiber laser cutting machine operation guide for users.
1. How to use the fiber laser cutting machine?
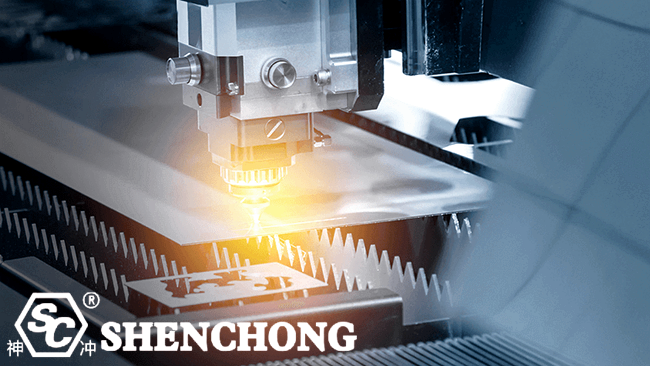
1) Preparation before starting
– Safety check
Wear protective equipment: Wear protective glasses, protective gloves and work clothes.
– Equipment Check
- Power supply check: Make sure the equipment is connected to a stable power supply.
- Cooling system: Check whether the coolant is sufficient and whether the cooling system is operating normally.
- Gas supply: Confirm that the auxiliary gas (such as oxygen, nitrogen) is sufficient and the pressure meets the requirements.
- Make sure the fiber optic cable is not damaged or bent excessively. Confirm that all fasteners and connectors are firm.
– Environmental preparation
Ensure that there are no flammable items in the work area.
Equip with necessary safety protection equipment, such as protective glasses, fire extinguishers, etc.
– Material preparation
Select appropriate material according to cutting requirements and clean the surface.
Fix the material on the workbench, making sure it is flat and firm.
2) Start the fiber laser cutting machine
- Turn on the main power: Turn on the main power switch of the device.
- Start the control system: Open the control panel of the cutting machine and wait for the system to complete initialization.
- Start the cooling system: Start the cooling system to ensure that the temperature control of the laser is normal.
3) Set cutting parameters
– Import cutting files
Import the design file (such as DXF or other CAD formats) into the control software.
Check whether the cutting path is correct and avoid overlapping or wrong paths.
– Adjust process parameters
Choose cutting mode:
Choose the appropriate cutting mode (such as carbon steel, stainless steel, aluminum alloy, etc.) according to the material type and thickness.
Laser power:
Choose the appropriate power according to the material type and thickness.
Cutting speed:
Adjust the speed to obtain the best cutting quality.
Auxiliary gas:
- Nitrogen: used for materials such as stainless steel and aluminum, with smoother cutting edges.
- Oxygen: used for carbon steel to improve cutting efficiency.
- Air: suitable for cutting needs with lower costs.
Focus position:
Adjust the focus according to the material thickness to ensure that the laser energy is concentrated.
5) Test cutting and cutting
– Test cutting
Carry out test cutting on the corners of the material and observe the cutting effect.
Adjust the power, speed, focus position and other parameters according to the test cutting results.
– Formal cutting
After confirming that all settings are correct, start the cutting program.
Monitor the cutting status during the cutting process and pay attention to any abnormalities (such as abnormal sparks, incomplete cutting, etc.).
6) Post-operation processing
– Check the cutting quality
The edges are smooth and burr-free.
The cutting size meets the design requirements.
Clean the workbench: remove residues and waste, and keep the equipment clean.
– Turn off the equipment
Turn off the laser, cooling system and control system.
Disconnect the main power supply.
7) Maintenance and care
- Daily inspection: clean the optical lens, check the optical fiber, cable and other components.
- Regular maintenance: replace the coolant, clean the laser, check the gas pipeline.
- Record log: record the equipment usage and maintenance records.
8) Other points to note
- Safety protection: avoid looking directly at the laser beam during laser cutting; non-operating personnel stay away from the equipment.
- Environmental requirements: keep the working environment dry and dust-free.
- Emergency treatment: In case of abnormal situation, press the emergency stop button immediately, shut down the equipment and troubleshoot the problem.
Fiber laser cutting machines are high-precision tools used for cutting various materials like metal, plastic, and composites. By following this guide, you can ensure safe and effective operation of your fiber laser cutting machine while maintaining optimal performance and longevity.
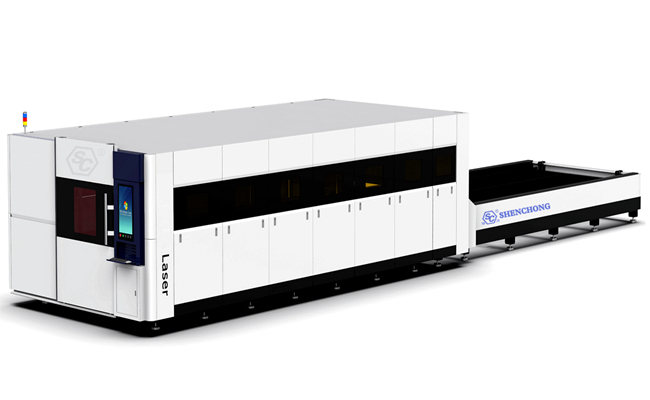
2. Fiber Laser Cutting Machine Operation Precautions
When using a fiber laser cutting machine, you also need to pay special attention to the following matters to ensure safe and efficient operation.
1) Safety protection
Wear protective glasses:
When operating a laser cutting machine, laser protective glasses must be worn to prevent the laser beam from shining directly into the eyes. They should be worn even when the laser cutting machine is in standby or turned on.
Avoid looking directly at the laser beam:
The laser beam is extremely hot during the cutting process, and direct exposure to the laser beam may cause serious injuries. Never look directly at the cutting head, especially when cutting.
Work area protection:
Make sure there are appropriate safety barriers around the laser cutting machine to prevent non-operating personnel from approaching the laser work area. Most equipment has safety protection devices, such as laser protection glass or protective covers.
2) Environmental requirements
Good ventilation:
The laser cutting process will produce a certain amount of exhaust gas, smoke and dust, so it is necessary to ensure that the work area has a good ventilation system or smoke extraction system to avoid the accumulation of harmful gases.
Temperature control:
Maintain a moderate working environment temperature for the laser cutting machine to avoid excessively high or low temperatures that affect the normal operation of the laser and cooling system.
Humidity control:
Excessive humidity may cause damage to electrical equipment, and too low humidity may cause static interference, so an appropriate humidity level should be maintained.
3) Equipment maintenance
Check the laser regularly:
The laser is the core component of the fiber laser cutting machine. Check the status of the laser regularly to ensure that the fiber connection is intact and there is no damage or stains. Damaged fiber may cause the laser beam to be unstable or malfunction.
Clean the optical lens and protective mirror:
During the laser cutting process, the optical lens and protective mirror are prone to accumulate smoke, dust and impurities, affecting the quality of the laser. Clean the lens regularly to ensure the stability of laser beam transmission and cutting accuracy.
Check the cooling system:
The normal fiber laser cutting machine operation of the cooling system is crucial for the laser cutting machine. Check the coolant level regularly to ensure that there is no leakage in the cooling system and keep the temperature of the laser within the normal range.
Check the gas supply system:
Ensure that the auxiliary gas supply such as oxygen, nitrogen, and air is sufficient, and there is no leakage in the pipeline, and the gas pressure meets the cutting requirements.
4) Operation precautions
Material preparation:
Before starting cutting, make sure the surface of the material is clean and flat. Remove debris such as oil, iron filings, rust spots, etc. to avoid affecting the cutting quality.
Focus adjustment:
Make sure that the laser focus point is accurately adjusted to the surface of the material. Inappropriate focus position will result in poor cutting effect or incomplete cutting. Most fiber laser cutting machines are equipped with autofocus function, but manual adjustment may also be required in certain cases.
Avoid reflective materials:
Be especially careful when cutting highly reflective materials (such as aluminum, copper, etc.). High reflectivity may cause the laser beam to reflect, damage the equipment or affect the cutting effect. When cutting such materials, select appropriate auxiliary gas and adjust the laser power and cutting speed as needed.
5) Monitoring during cutting
Monitor the cutting process:
During the cutting process, pay attention to the cutting effect, such as whether the cutting edge is flat, whether there are any abnormal phenomena (such as too many sparks or uneven cutting effect). If there is an abnormality, stop cutting immediately and check the equipment.
Temperature monitoring:
During the laser cutting process, the internal temperature of the equipment may rise, especially the temperature of the laser and cooling system. Keep the temperature within the normal range to prevent overheating and damage to the equipment.
Equipment alarm system:
Many fiber laser cutting machines are equipped with an alarm system, which will sound an alarm when the equipment is abnormal. If a fault occurs, stop the operation immediately and check the cause.
6) Operator requirements
Professional training:
Before operating the fiber laser cutting machine, the operator should receive professional training and be familiar with basic knowledge such as fiber laser cutting machine operation, maintenance, and troubleshooting.
Non-operating personnel are prohibited from entering:
During the laser cutting process, unauthorized personnel are prohibited from entering the operating area, especially the cutting area.
7) Emergency stop
Emergency stop button:
During the operation of the equipment, if a fault or emergency occurs, the emergency stop button should be pressed immediately to prevent the equipment from causing greater damage or accidents.
Abnormal handling:
If the equipment has abnormal conditions during the cutting process (such as abnormal sparks, overheating or laser abnormality), it should be stopped immediately for inspection and the fault should be eliminated before fiber laser cutting machine operation.
3. Summary
Compared with traditional laser cutting machines, fiber laser cutting machines have many advantages, such as higher cutting speed, lower maintenance cost, and smaller laser beam focus, which can cut finer graphics. It is widely used in the cutting of metal materials, especially in the industrial processing of metals such as stainless steel, carbon steel, and aluminum alloy.
Fiber laser cutting machine is a high-precision equipment, which requires strict compliance with safety regulations and regular maintenance during operation. Through correct operating procedures, environmental control and equipment maintenance, the efficient operation and cutting quality of the equipment can be guaranteed, and the service life of the equipment can be effectively extended.
Follow the above steps to complete the work of the fiber laser cutting machine safely and efficiently. If you have special needs, please refer to the equipment manual or contact technical support.
Other machine operation guide for users: