Table of Contents
Press brake machine is a mechanical device used to bend metal sheets into specific shapes. In order to ensure the normal operation and prolong the service life of the press brake machine, maintenance and upkeep work is particularly important. This article introduces 21 press brake maintenance items and operating procedures for press brake operators to study.
21 Press Brake Maintenance Items
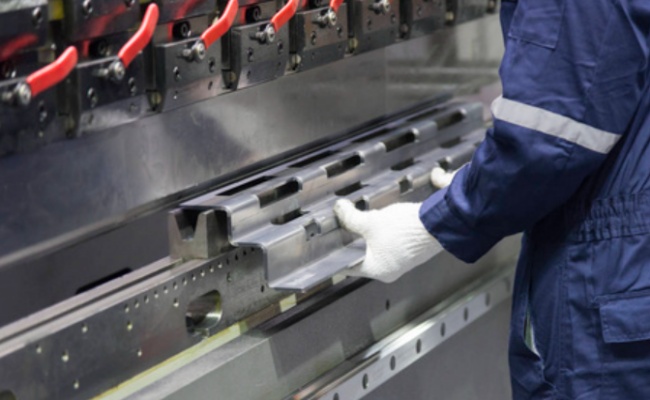
Maintenance Of The Machine Frame
- Regularly clean the debris and dust on the machine frame, and maintain a dry and clean working environment to reduce malfunctions in various parts of the machine.
- Check the connecting bolts of the machine frame, tighten them if they are loose, and lubricate them with appropriate lubricants.
Maintenance Of Guide Rails
- Regularly check the wear of the guide rail, and replace it in a timely manner if there is any wear.
- Clean the dust and debris on the guide rail and lubricate it with appropriate lubricant.
- Regularly check the parallelism and perpendicularity of the guide rail, and adjust it in a timely manner if there are any problems.
Maintenance Of Oil System
- Regularly clean the filters and pipelines in the oil system and check for oil leaks.
- Regularly replace the lubricating oil and hydraulic oil in the machine, and clean the corresponding oil tank during replacement.
- Regularly check the oil level and quality in the oil system, and adjust or replace it promptly if there are any problems.
Maintenance Of Electrical System
- Regularly clean the contactors and relays in the electrical system to ensure its normal operation.
- Regularly inspect the cables and wiring harnesses in the electrical system, and replace them promptly if they are aged or damaged.
- Regularly check the fuses and circuit breakers in the electrical system to ensure their proper functioning.
Maintenance Of Press Brake Tools
- Regularly inspect and replace theupper punch and lower dieson the press brake machine to ensure their sharpness and accuracy.
- Clean the cutting chips and debris on the press braketools and lubricate them with appropriate lubricants.
- Regularly check the bendingquality and bendingspeed of the press brake tools, and adjust them in a timely manner if there are any problems
Maintenance Of Hydraulic System
- Regularly inspect the hydraulic cylinders and pumps in the hydraulic system, and adjust or replace them promptly if there is oil leakage or looseness.
- Clean the oil pipes and oil pipe joints in the hydraulic system and check for oil leakage.
- Regularly check the pressure and flow rate of the hydraulic system, and adjust them promptly if there are any problems.
Maintenance Of Safety System
- Regularly check the sensors and switches in the safety system to ensure the safety performance of the bending machine.
- Clean the infrared and photoelectric switches in the safety system and adjust their sensitivity.
- Regularly check the emergency stop switch and protection amount in the safety system, and adjust or replace them in a timely manner if there are any problems.
Training Of Operators
- Train and guide operators on the correct use and maintenance of the bending machine, ensuring its proper operation and avoiding malfunctions caused by mis-operation.
Correct Usage Steps Of CNC Press Brake
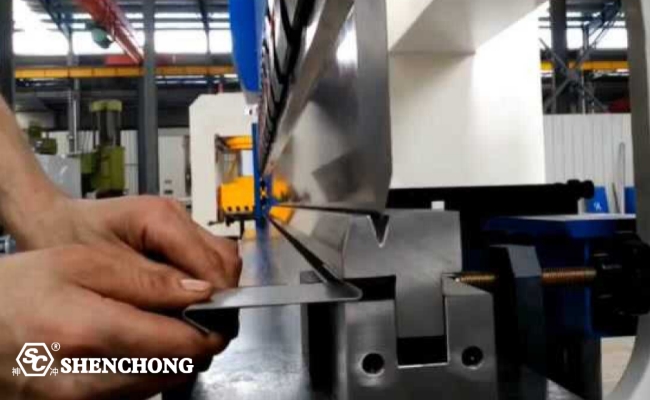
- Connect power: Turn on the power switch on the control panel of the CNC press brake machine, and then start the oil pump. When the oil pump is successfully started and the sound of the oil pump rotating is heard, it indicates that the bending brake machine can work normally.
- Test schedule: After the hydraulic press brake machine can start normally, it needs to be tested to ensure that it can complete its work properly. This includes testing whether there is a gap in the thickness of the board when the upper mold descends to the bottom, in order to avoid damage to the press brake machine’s mold and extend its service life. Travel adjustment is divided into automatic adjustment and manual adjustment, and users can choose according to their own needs.
- Determine slot size: After testing and adjusting, users need to choose the bent slot size based on the cutting standards of the board. In general, it is possible to choose a slot width 8-10 times the thickness of the metal sheet plates, but there may be differences between different machines.
- Preheating: Preheating should be carried out before the formal operation of the machine tool every day. During the preheating process, it is necessary to check whether each device is functioning properly.
- Preparation for operation: Before operating the machine tool, it is necessary to fully master the relevant procedures and steps in the operation manual. At the same time, it is necessary to check the set values of all measuring instruments and the status of moving parts. When carrying heavy objects, forklifts, cranes, or multiple people should be used in cooperation. Work lights can become very hot after prolonged use, so do not touch them. Do not operate incorrect switches and buttons. Before operation, be sure to visually confirm the switches on the control panel. When loading and unloading workpieces, make sure to completely stop the machine tool from running.
- Automatic operation: During the operation of the machine tool, it is necessary to fully master the relevant procedures and steps in the operation manual. Do not rely on the machine tool and do not operate incorrect switches and buttons. When it is absolutely necessary for two or more personnel to operate simultaneously, all participants must communicate and cooperate closely with each other.
- Programming and trial bending: Arrange the program according to the bending sequence and bending size. There are usually two input methods, angle input and depth input, with depth input being more commonly used. Enter the CNC control systeminto memory mode and input values such as bending size L, D value, Z value, speed, time, and number of times. Then conduct product trial folding, and after the trial folded products are checked to be correct, they can be mass-produced.
Please note that when operating the CNC press brake, it is necessary to follow relevant safety regulations and operating procedures to avoid unnecessary injuries caused by illegal operations. At the same time, regular maintenance and upkeep of the equipment should be carried out to ensure its normal operation and extend its service life.
Press Brake Safety Operating Procedures
- Strictly abide by the safety operating procedures for machine tool workers and wear labor protection equipment according to regulations.
- Before starting, it is necessary to carefully check whether the motor, switch, circuit, and grounding are normal and secure, and check that all operating parts and buttons of the equipment are stuck in the correct position.
- Check the overlap and firmness of the upper and lower molds; Check whether each positioning device meets the requirements for processing.
- When the skateboard and all positioning axes are not at the origin, run the return to origin program.
- After the equipment is started, it should be idle for 1-2 minutes, and the skateboard should be fully moved 2-3 times. If any abnormal sound or malfunction is found, the vehicle should be stopped immediately, the fault should be eliminated, and everything should be normal before it can work.
- During work, one person should be in charge of unified command to ensure close cooperation between the operator and the feeding and pressing personnel, and to ensure that all cooperating personnel are in a safe position before issuing the bending signal.
- When bending the sheet metal, it must be compacted to prevent the sheet metal from lifting and injuring people during bending.
- When adjusting the sheet metal pressing mold, the power must be cut off and the operation must be stopped before proceeding.
- When changing the opening of the variable lower mold, no material is allowed to come into contact with the lower mold.
- When the machine tool is working, no one is allowed to stand at the rear of the machine tool.
- It is strictly prohibited to press the folded plate material separately at one end.
- If the workpiece or mold is found to be misaligned during operation, it should be stopped for calibration. It is strictly prohibited to use hands to calibrate during operation to prevent hand injury.
- It is prohibited to fold excessively thick iron plates or quenched steel plates, high-grade alloy steels, square steels, and plates that exceed the performance of the plate bending machine, in order to avoid damaging the machine tool.
- Regularly check the overlap of the upper and lower molds; Whether the indication of the pressure gauge complies with the regulations.
- Immediately stop the machine in case of any abnormality, check the cause and promptly eliminate it.
- Before shutting down, place wooden blocks on the lower mold below the oil cylinders on both sides to lower the upper sliding plate onto the wooden blocks.
- Exit the control system program first, and then cut off the power.
Conclusion
The maintenance and upkeep of the press brake play an important role in the normal operation and extended service life of the equipment. By regularly cleaning, lubricating and maintaining, inspecting and repairing, paying attention to safety precautions, and storing and protecting, the bending machine can be effectively maintained in good condition, improving production efficiency, and reducing the risk of equipment failure and damage.