Table of Contents
Laser Welding Overview
Laser welding, as a modern welding technology, has advantages such as deep penetration, fast speed, small deformation, high power density, and is not affected by magnetic fields. It is widely used in high-end precision manufacturing fields such as automobiles, ships, and aerospace. This article mainly introduces the laser welding principle, advantages and disadvantages, helping people who have not used laser welding to have a preliminary understanding of this welding technology.
Laser Welding Principle
Laser welding can be achieved using continuous or pulsed laser beams, and the principle of laser welding can be divided into heat conduction welding and laser deep penetration welding.
- A power density of less than 104-105 W/cm2 is considered as thermal conduction welding, where the depth of fusion is shallow and the welding speed is slow; The principle of laser welding is: laser radiation heats the surface to be processed, and the surface heat is guided to the interior for diffusion through heat transfer. By controlling parameters such as the width, energy, power, and frequency of the laser pulse, the workpiece is melted to form a specific molten pool.
- Laser deep penetration welding generally uses a continuous laser beam to connect materials, and its metallurgical physical process is very similar to electron beam welding. The energy conversion mechanism is achieved through small holes. Under the irradiation of high-power density laser, the material evaporates to form small holes, which are filled with vapor like a blackbody and absorb almost all of the incident light energy. Heat is transferred from the outer wall of the high-temperature cavity, causing the metal surrounding the cavity to melt. Under the irradiation of a light beam, the wall material continuously evaporates to produce high-temperature steam. The surface tension of the wall layer formed by the flow of liquid outside the hole wall is in constant equilibrium with the steam pressure continuously generated inside the hole cavity. The light beam continuously enters the small hole, which is always in a stable state of flow. The molten metal surrounding the hole wall moves forward with the leading light beam, filling the gap left by the small hole and condensing accordingly, thus forming a weld seam.
Application Field Of Laser Welding
Laser welding has been widely used in various industries, such as:
- Automotive industry: Laser welding can achieve efficient and precise connection of automotive components, improve productivity and quality, reduce costs and pollution. Laser welding can be used for welding components such as car bodies, chassis, engines, transmissions, exhaust pipes, airbags, instrument panels, etc. For example, laser welding can achieve integrated design of car tailgates, reduce the number and weight of parts, improve rigidity and strength, and enhance appearance and safety.
- Shipbuilding: Laser welding can be used for connecting ship plates, solving the problems of warping and deformation in traditional welding, improving the quality and strength of welds, and reducing material consumption and labor costs. Laser welding can be used for welding ship structures, decks, bulkheads, bilges, pipelines, and other components. For example, laser welding can achieve rapid assembly of large ship structures, shorten construction cycles, and improve production efficiency.
- Home field: Laser welding can be used for the manufacturing of all aluminum homes, achieving seamless connection of aluminum alloy profiles, improving the aesthetics and durability of homes, and meeting the needs of environmental protection and health. Laser welding can be used for the production of home products such as all aluminum wardrobes, all aluminum bookcases, and all aluminum shoe cabinets. For example, laser welding can achieve zero formaldehyde, zero pollution, and recycling value in all aluminum homes, creating a new concept of green and fashionable home furnishings.
Classification Of Laser Welding
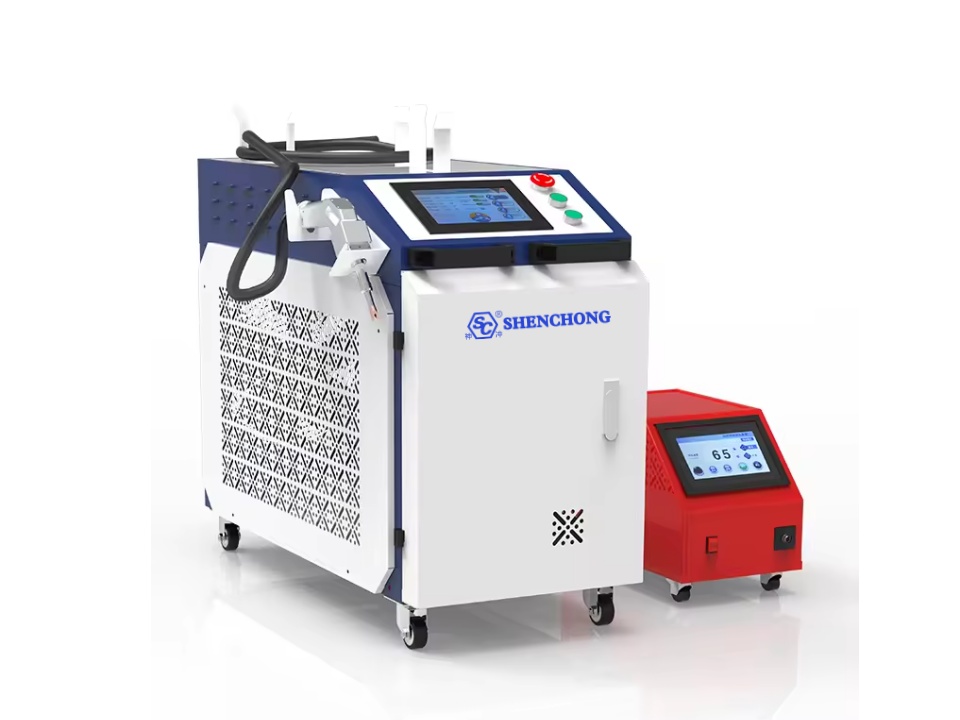
According to the different energy output modes of lasers, laser welding can be divided into continuous laser welding and pulsed laser welding. Continuous laser welding forms a continuous and uninterrupted weld morphology during the welding process, while pulse laser welding forms a circular weld spot on the surface of the welded workpiece due to the discontinuous energy input to the surface of the workpiece. Different weld morphologies can be obtained based on the changes in the laser parameters. According to the different power densities of the laser focused spot, laser welding can be divided into thermal conductivity welding and deep penetration welding.
1. Laser Thermal Conductivity Welding
The power density of the laser thermal conductivity welding spot on the surface of the workpiece is relatively low, generally less than 105W/cm2. Laser delivers energy to the surface of the welded workpiece, heating the metal surface to a temperature between the melting and boiling points. The surface of metal materials converts the absorbed light energy into heat energy, causing the temperature of the metal surface to continuously rise and melt. Then, the heat energy is transferred to the interior of the metal through thermal conduction, gradually expanding the melting area. After cooling, a welding point or weld is formed. This welding principle is similar to tungsten inert gas arc welding (TIG), known as thermal conductivity welding.
2. Laser Deep Penetration Welding (Small Hole Welding)
When the laser power density applied to the metal surface is greater than 105W/cm2, the high-power laser beam acts on the surface of the metal material, causing local melting and forming “small holes”. The laser beam penetrates into the interior of the molten pool through the “small holes”, while the metal melts in front of the small holes. The molten metal flows around the small holes to the back, re solidifies, and forms a weld seam.
Advantages And Disadvantages Of Laser Welding
Laser welding is an efficient and precise welding method that uses a high-energy density laser beam as a heat source. Laser welding is one of the important aspects of laser material processing technology application, widely used in fields such as automotive, aerospace, electronics, and medical. It has the advantages of fast speed, high quality, high flexibility, and green environmental protection.
So, what are the advantages of laser welding compared to traditional welding methods? What are the difficulties encountered during laser welding and how can they be solved? What are the common application areas for laser welding?
Advantages Of Laser Welding
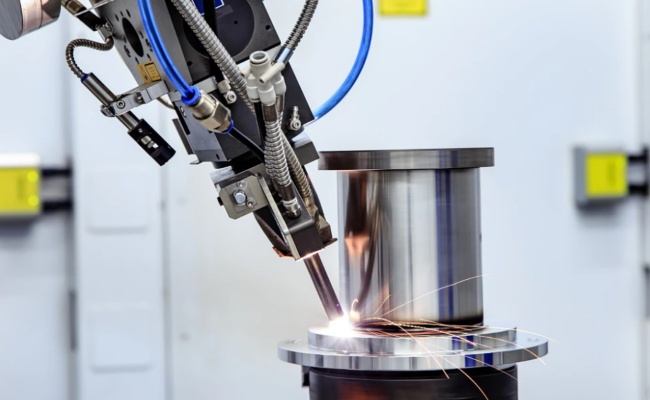
Compared to traditional welding methods, laser welding has the following advantages:
- Fast speed, deep depth, and small deformation. Laser welding has high energy density, fast heating and cooling rates, small heat affected zone, and low welding stress and deformation. Laser welding can achieve high aspect ratio welds, with a maximum of 10:1.
- Non contact processing, high flexibility. Laser welding does not require contact with the workpiece, nor does it require electrodes or filler materials, which can reduce pollution and losses. Laser welding can be transmitted and transformed through optical components, making it easy to cooperate with robots and achieve automation and multi station processing. Laser welding can also be performed at room temperature or under special conditions, suitable for welding difficult to access parts or refractory materials.
- High quality and good performance. Laser welding, due to its low heat input and fast cooling rate, can reduce defects such as porosity and cracks, and improve the density and strength of the weld seam. Laser welding can also achieve the connection of different metals or dissimilar materials, improving the structure and properties.
- Green and environmentally friendly, safe and pollution-free. Laser welding does not produce harmful gases or noise, is not affected by electric or magnetic fields, and is harmless to human health and the environment.
Difficulties And Solutions In Laser Welding
Although laser welding has many advantages, there are still some problems during welding:
- Welding spatter: refers to the appearance of many metal particles on the surface of the material after welding is completed, which adhere to the surface of the material. This will affect the surface quality of the weld seam and also contaminate and damage the lens. The reason for splashing may be that the surface of the material is not clean, there are oil stains or pollutants, or the volatilization of the galvanized layer.
The solution is to clean the material surface before welding, reduce welding energy appropriately, and minimize spatter.
- Cracks: Refers to thermal cracks generated by continuous laser welding, such as crystal cracks, liquefaction cracks, etc. The main reason for cracking is the excessive shrinkage force of the weld before it fully solidifies.
The solution is to use measures such as wire filling and preheating to reduce or eliminate cracks.
- Pores: Refers to the appearance of pores on the surface of the weld seam. The reason for the formation of pores may be that the laser welding melt pool is deep and narrow, with a fast cooling rate, and the gas generated in the liquid melt pool cannot escape in time; Either the surface of the weld seam is not cleaned thoroughly, or zinc vapor evaporates from the galvanized sheet.
The solution is to clean the surface of the weld seam, improve the volatilization of zinc when heated, and adjust the blowing direction.
- Edge biting: refers to poor bonding between the weld and the base metal, resulting in a groove with a depth greater than 0.5mm, a total length greater than 10% of the weld length, or a length greater than the acceptance standard requirements. The reason for the occurrence of undercutting may be that the welding speed is too fast, which prevents the liquid metal from redistributing on the back of the small hole; Or the gap between the joint assembly may be too large, resulting in a decrease in molten metal in the filling process; Or the energy drop time at the end of laser welding is too fast, causing the small hole to collapse.
The solution is to control the matching of laser welding machine processing power and speed to avoid edge biting; Polish, clean, and repair the bite edges found during inspection.
Conclusion
Laser welding is a high-precision and high-efficiency welding technology with broad application prospects. Different welding methods and application scenarios require the selection of different laser welding methods to achieve the best welding effect. Laser welding technology is still constantly developing and innovating, and there will be more new types of lasers and processes emerging in the future, providing higher quality, higher efficiency, and lower cost welding solutions for various industries.