Table of Contents
In industrial production, common high reflective materials such as copper and aluminum require frequent processing, but for many fiber laser cutting equipment manufacturers, the cutting process of high reflective materials is often challenging and difficult to solve. Many sheet metal fabricators often inquire about the capability of fiber laser cutting machines to cut high-reflective materials such as aluminum and copper. This article will explore how fiber laser cutting machines handle these reflective materials and introduce some advanced technologies and best practices.
What Is A Laser Cutting Machine
A laser cutting machine is a mechanical device that uses a laser beam for cutting. The laser cutting machine focuses the laser beam into a high-power density beam and irradiates it onto the surface of the workpiece, causing the material to reach its melting or boiling point. At the same time, high-pressure gas is used to blow away the melted or vaporized metal, ultimately forming a cutting seam and achieving the purpose of cutting.
Characteristics And Application
Laser cutting machines have the following characteristics:
- High precision: The diameter of the laser beam is very small, the cutting accuracy is high, and the incision is smooth.
- Fast speed: Laser cutting has fast speed and high efficiency.
- Not limited to patterns: Not limited to traditional cutting patterns, it can automatically layout and save materials.
- Small heat affected zone: During the cutting process, the deformation of the board is small and the cutting seam is narrow.
- No mechanical stress: The incision has no mechanical stress and no shear burrs.
- Low processing cost: suitable for large-scale production, with low processing cost.
- Laser cutting machines are mainly used for cutting metal and non-metal materials, especially suitable for precision machining and high demand production environments.
Understand Reflective Metal Materials
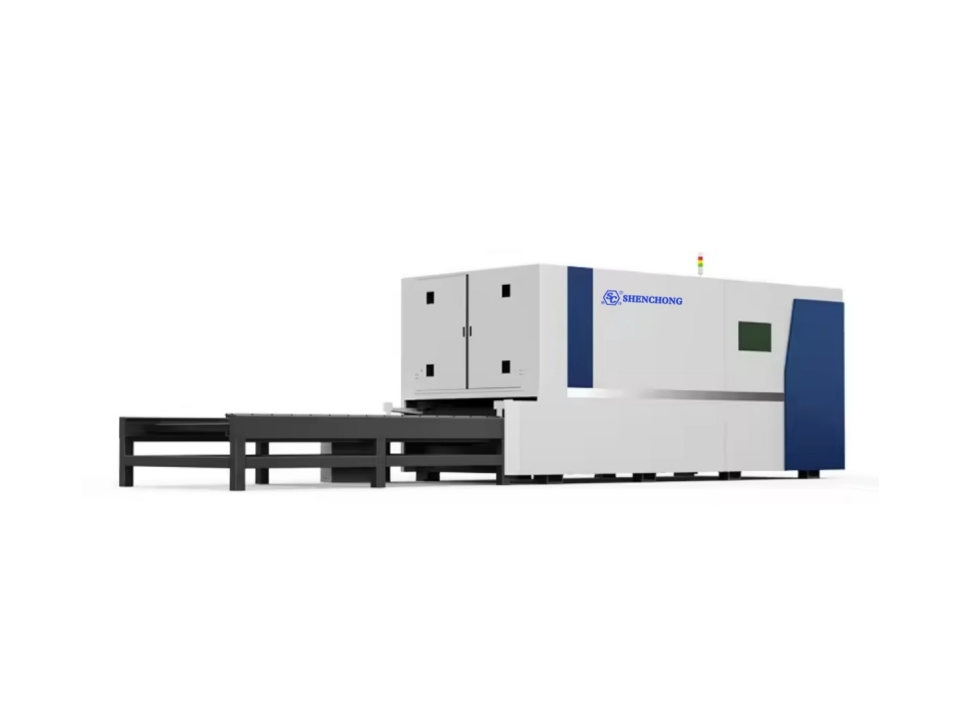
Why is Laser Cutting Highly Reflective Metals Challenging?
Highly reflective metal materials include gold, silver, copper, and aluminum. These materials have very high reflectivity and are commonly used in applications that require high reflectivity. These materials have high reflectivity and may cause the beam to reflect back to the laser source during laser cutting, potentially causing damage to the equipment. In addition, reflective materials can also affect the efficiency and quality of cutting.
What Are High Reflectivity Metal Materials?
The reflectivity of gold, silver, and copper is very high, especially copper, which has a reflectivity of up to 95% for lasers with a wavelength of 1064nm. These materials are commonly used to make optical components such as mirrors because they have the highest mirror reflectivity. In addition, after blackening treatment, steel can also absorb more than 80% of laser power, indicating that surface treatment of the material has a significant impact on its reflectivity.
Highly reflective metal materials have a wide range of applications in various fields. For example, in fields such as lighting, imaging, aerospace, and military, high reflective materials can improve the resolution and imaging quality of optical systems. High reflective materials can also achieve ideal optical effects in buildings, road lighting, and traffic signals. In addition, high reflective coatings are also applied to aircraft engine nozzles and satellite antennas to improve infrared thermal radiation efficiency and enhance stealth performance.
- Copper: Copper has extremely high thermal conductivity and reflectivity, making it difficult for laser energy to concentrate in the cutting area. Copper has a low absorption rate for laser beams, usually less than 30%, which is equivalent to 70% of the laser being reflected. This not only causes energy loss and waste, but also easily damages components such as processing heads, lenses, and laser generators.
- Brass: Brass is an alloy mainly composed of copper and zinc, but due to its zinc content, it releases toxic smoke during cutting and requires special treatment. Brass is a highly reflective metal material with extremely low absorption rate for ordinary wavelength lasers. It also has good thermal conductivity. The absorbed heat will quickly spread to the surrounding area of the processing zone, affecting the processing quality.
- Stainless steel: Although stainless steel has a lower reflectivity than aluminum and copper, it exhibits reflective properties after polishing. Its surface smoothness and oxide layer may make cutting more difficult and easily lead to problems such as sheet burns.
- Aluminum: Due to its high reflectivity and thermal conductivity, aluminum is difficult to process during laser cutting. Pure aluminum is more difficult to cut than iron-based metals due to its low melting point and high thermal conductivity. Coating or alloying can improve cutting effectiveness, efficiency, and safety.
Challenges of Cutting Reflective Materials
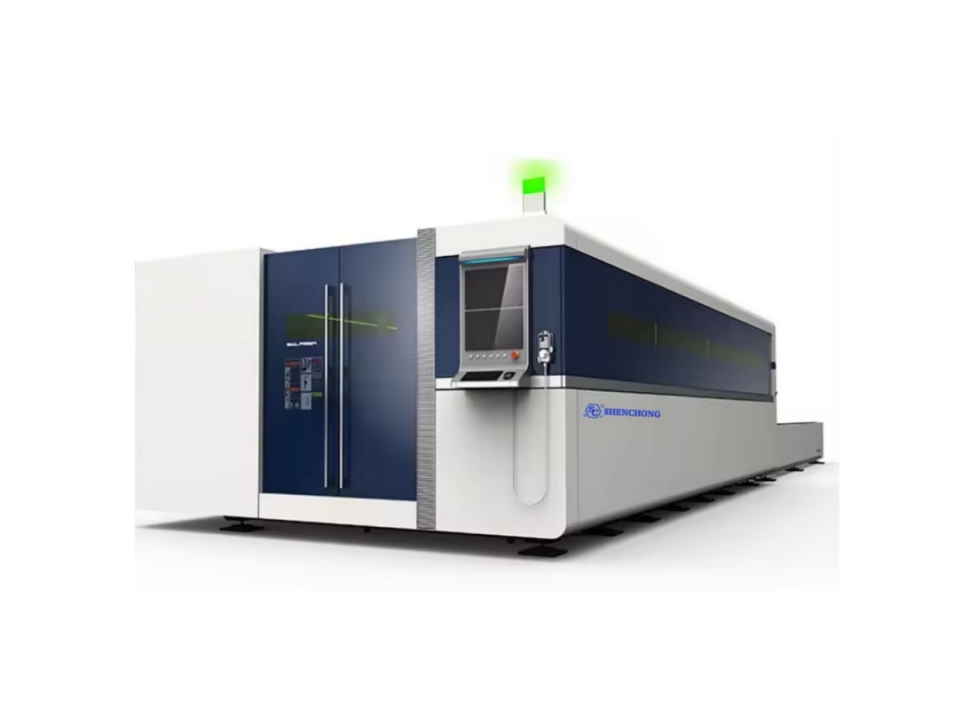
Challenge 1: Beam Reflection
Reflective materials such as aluminum and stainless steel have high reflectivity. They will reflect some of the laser beam back to the laser source, which not only reduces cutting efficiency but also causes damage to the laser generator, especially the laser lens and reflector system.
Solution
- Choose a fiber laser cutting machine equipped with a self-protection system. When laser beam reflection is detected, the laser source can be automatically turned off to prevent equipment damage. Compared with CO2 laser cutting machines, fiber laser cutting machines use optical fibers to transmit laser beams, reducing complex reflection systems and thus lowering the risk of beam reflection.
- Cover the surface of the reflective material with a special coating. These coatings can absorb laser beams and reduce laser beam reflections.
Challenge 2: Laser Cutting Quality
Due to its high reflectivity, reflective metal materials can to some extent affect cutting accuracy and quality.
Solution
- Use appropriate auxiliary gases and cutting parameters during the cutting process.
- Choose a high-precision fiber laser cutting machine to improve cutting accuracy and quality by precisely controlling the focus and motion path of the laser beam.
Challenge 3: Heat Dissipation
Materials with high thermal conductivity, such as copper, quickly dissipate heat during laser cutting, making it difficult for laser energy to concentrate in the cutting area, resulting in insufficient cutting depth or reduced cutting speed.
Solution
Optimize laser cutting parameters, such as increasing laser power, reducing cutting speed, etc., to ensure sufficient laser energy is concentrated in the cutting area.
Use auxiliary gases (such as nitrogen, argon, etc.) for cutting. These gases can not only help blow away molten metal, but also reduce heat conduction to a certain extent.
Preheat the material before cutting to reduce its thermal conductivity and minimize heat loss, making it easier for laser energy to concentrate in the cutting area and improve cutting efficiency.
Using short pulse or ultra short pulse laser technology to reduce heat accumulation and improve cutting quality.
Challenge 4: Oxidation And Surface Pollution
Aluminum and other materials are prone to oxidation to form compounds such as aluminum oxide, which can adhere to the surface of the material and the cutting edge, affecting the cutting effect.
Solution
Pre-treat the material before cutting to remove oxides and surface impurities to improve cutting efficiency.
During the cutting process, inert gases (such as nitrogen) are used as protective gases to reduce the occurrence of oxidation reactions.
Choose cutting parameters and process methods with antioxidant properties, such as pulsed laser cutting.
Reflective Metal Material Cutting Technology
Auxiliary Gas
- Oxygen: When cutting steel and other metals, oxygen can be used as an auxiliary gas to increase cutting speed. Oxygen reacts chemically with high-temperature metals, producing an exothermic oxidation effect that further accelerates the cutting process of the material.
- Nitrogen: Nitrogen is very useful when cutting easily oxidizable materials such as aluminum. It can prevent the material from being oxidized during the cutting process, maintaining the smoothness and accuracy of the cutting edge. In addition, nitrogen can also reduce the emission of smoke and harmful gases during the cutting process.
- Argon gas: Argon gas is suitable for cutting materials such as brass. It has good inertness and can protect the material from oxidation during the cutting process. Meanwhile, argon gas can also reduce the generation of smoke and harmful gases during the cutting process, improving the working environment.
Auxiliary gas undoubtedly enhances the cutting effect.
Through the chemical reaction between auxiliary gas and metal material, it enhances the cutting ability.
Helps the equipment blow away the slag from the cutting area to clean the slit.
Cools the area around the cut and protects the focusing lens.
When laser cutting copper, the introduction of an auxiliary gas will react with the metal at high temperatures to improve cutting speed and effectiveness. The use of O₂ can aid combustion and improve efficiency. As for laser cutting equipment, N₂ is a common auxiliary gas to enhance the cutting effect, of course, for copper plate below 1mm, no auxiliary gas is needed for cutting and processing. But when the thickness of copper reaches 2mm, N₂ can no longer achieve the expected processing effect. In this case, oxygen must be used to oxidize the copper for smooth cutting.
Anti-Reflection Solution
Protective coating: Pre coating a layer of anti reflective coating on the surface of high reflective materials can significantly reduce the reflectivity of the laser beam, allowing more laser energy to be absorbed by the material, thereby improving cutting efficiency and effectiveness. This coating needs to have good performance, such as high temperature resistance and corrosion resistance, to ensure stability during laser cutting process.
Beam cutting: Beam cutting technology interrupts the optical path of the laser beam before it is reflected to the laser source, effectively preventing damage to the laser generator caused by reflected light. By installing a beam trap, reflected light can be captured to ensure that the laser energy mainly acts on the material, reducing the damage caused by reflection to the equipment.
High Power Laser Generator
During the cutting process of highly reflective materials, piercing technique is crucial. To maximize power density and accelerate melting speed, the focal point should be positioned as close to the material’s surface as possible. This minimizes the number of interactions between the beam and the material surface, allowing the beam to more effectively melt the material.
Copper (Cu) and silver (Ag) are highly reactive materials to 1070 nm fiber lasers, with low absorption rates, much lower than iron (Fe) and steel. However, their absorption rates are relatively higher for solid-state lasers. Therefore, choosing the right type of lasers may make cutting highly reflective materials easier.
Improving power output: Using a higher power laser generator is a direct method for processing highly reflective materials. Higher power means stronger penetration and deeper cutting depth, which can more effectively overcome the material’s reflectivity.
Power modulation: By dynamically adjusting the power output of the laser, precise control can be achieved based on the reflectivity of the material and cutting requirements. This adjustment ensures that the laser energy remains at its optimal state throughout the cutting process, improving cutting quality and efficiency.
Pulse modulation
Controllable pulse: Using controllable pulse technology, a continuous laser beam can be divided into a series of short pulses and strong pulses. This pulse mode can reduce the accumulation of heat in the material, prevent deformation or melting due to overheating, and thus improve cutting accuracy and edge quality.
Short pulse: Short pulse lasers have higher peak power and shorter duration, which can heat and evaporate materials faster and achieve more precise cutting. Meanwhile, short pulses can also reduce the heat affected zone and protect the surrounding structures of the material from damage.
Advanced Technology Of Fiber Laser Cutting Machine
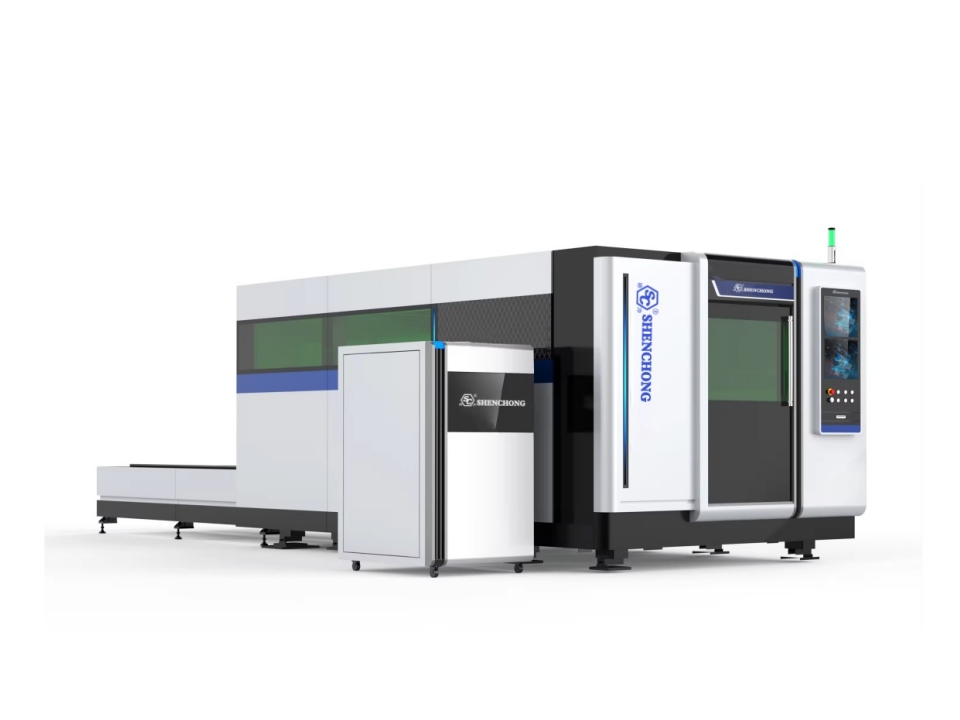
Real Time Monitoring
- Process control: Real time monitoring technology can obtain various parameters (such as temperature, speed, power, etc.) during the cutting process in real time, and dynamically adjust them according to preset process requirements to ensure the stability and controllability of the cutting process.
- Quality assurance: By monitoring the cutting effect in real-time (such as slit width, roughness, etc.), possible quality issues can be detected and corrected in a timely manner to ensure the quality of the cut products.
- Real time monitoring technology monitors the entire cutting process through sensors and monitoring systems integrated into fiber laser cutting machines, ensuring automatic adjustment of parameters during the cutting process and ensuring stable quality. This technology can prevent incorrect operations, maintain cutting accuracy, and improve overall production efficiency.
Adaptive Optics
- Auto focusing: By optimizing the focusing system, adaptive optics technology can significantly improve the focusing accuracy and energy density of laser beams, thereby enhancing cutting quality and efficiency.
- Real time adjustment: Adaptive optics technology can monitor the focusing state of the laser beam in real time and make real-time adjustments based on feedback signals to ensure that the laser beam is always in the optimal focusing state.
The adaptive optics system dynamically optimizes the focus of the laser beam by adjusting the optical system in real-time, ensuring better adaptation to materials of different thicknesses or reflections during the cutting process. This adjustment can reduce the reflection loss of the laser beam, improve cutting accuracy and efficiency.
Beam Shaping
Beam shaping technology can customize the laser beam profile according to different cutting requirements, thereby optimizing the energy distribution of the laser beam and improving cutting efficiency and quality.
Improve power utilization: Shaping laser beams can better match the absorption characteristics of cutting materials, improve the utilization of laser energy, and reduce energy waste.
Beam shaping technology allows customization of the shape of laser beams. The laser beam is shaped by specific optical elements (such as beam shaper, micro lens, etc.) to transform it from the original Gaussian distribution to the desired shape (such as circle, rectangle, square, etc.). Adapt to different cutting needs. This technology can improve energy efficiency, especially when processing high reflective materials, with significant effects, helping to improve processing efficiency and quality.
In summary, by adopting these advanced technologies, fiber laser cutting machine can effectively address the cutting challenges of reflective materials, improve cutting efficiency, accuracy, and quality.
Alternative Cutting Methods
Although fiber laser cutting machines have many solutions to cut reflective materials with high precision, many users still do not want to use the laser cutting machine as the first choice to cut these materials. By using the fiber laser cutting machine to cut some high reflective materials can cause deterioration of the material. In this case, they usually choose to use the traditional plate cutting method, which is plate shearing machine.
SC Machinery has the automatic front feeding plate shearing machine specially designed to cut large quantities of cobalt plates, nickel plates, and copper plates.
Conclusion
In this article, we provide insights on how to use laser cutting to cut reflective metals. Laser cutting machines are particularly suitable for processing highly reflective metals such as brass, aluminum, and silver, with precision and efficiency. Laser cutting will continue to be the good choice for processing highly reflective metals and will bring more convenience and benefits to metal processing in the manufacturing industry.