Table of Contents
The press brake machine is the foundation of the metal manufacturing field and is crucial for bending and forming metal sheets into various components used in industries such as automotive, aerospace, construction, electronics, and manufacturing. With the advancement of technology, the pattern of bending brake machines has undergone significant changes. Nowadays, two main types of bending machines dominate the market: CNC press brake machines and NC press brake machines.
Although both NC and CNC press brakes are highly effective in metal forming, they offer different functionalities, automation levels, precision, and adaptability. Understanding the differences between NC press brakes and CNC press brakes are crucial for manufacturers who want to improve operational efficiency, precision, and productivity.
In this detailed guide, we will introduce the main differences between NC and CNC bending brake machines, explore their control systems, functions, costs, and applications. At the end of this article, you will have a clear understanding of which type of bending machine is most suitable for your production needs.
Overview of NC Press Brakes and CNC Press Brakes
What is a NC Press Brake?
NC (Numerical Control) press brakes use a numerical control system to direct the machine’s movements and bending operations. In an NC system, operators input numerical values to control the positioning of the back gauge and ram. While NC press brakes offer basic automation capabilities, some manual intervention is still required to adjust machine settings between bends.
NC press brake is open loop machine, which means after operator input the value and machine runs, the controller would not receive the feedback signal.
NC press brakes are typically less expensive than their CNC counterparts and are often used in small to medium-sized production operations where basic bending tasks are performed. These machines can handle a variety of materials but are generally less suitable for highly complex or precision-demanding tasks.
What is a CNC Press Brake?
CNC (Computer Numerical Control) press brakes are highly advanced machines that use computerized control systems to automate the entire bending process. CNC press brakes allow for precise control over multiple axes (typically including the X, Y, R, and Z axes), enabling more complex bending operations. CNC press brakes often include advanced features such as real-time monitoring, automatic tool adjustment, and integration with CAD/CAM software.
CNC press brakes are designed for high-volume, high-precision applications where accuracy and repeatability are paramount. They are more expensive than NC press brakes but offer superior performance in terms of speed, efficiency, and versatility.
NC Press Brakes And CNC Press Brakes Differences In Control Systems
First of all, the control system is perhaps the most critical difference between NC and CNC press brakes, dictating how the machines are programmed and operated.
NC Control Systems
NC press brakes rely on a basic numerical control system where the operator manually inputs specific data into the machine. These data points typically include parameters like back gauge positioning, material thickness, and the angle of each bend. However, the control system is limited in its functionality, often allowing for the control of only two axes (X and Y). As a result, operators must manually adjust the machine for each new bending operation.
Key features of NC control systems include:
- Manual Data Input:Operators input numerical data for each bend, such as the bending angle, material thickness, and ram position.
- Limited Axis Control:Typically, NC press brakes control only two axes—the Y-axis for ram movement and the X-axis for back gauge positioning.
- Sequential Operation:The operator must enter and adjust data for each bend sequentially, requiring manual intervention between bends.
- Limited Program Storage:NC press brakes can store basic programs, but their memory capacity is limited, making them less suitable for complex, multi-bend projects.
Controller Introduction (Estun E21)
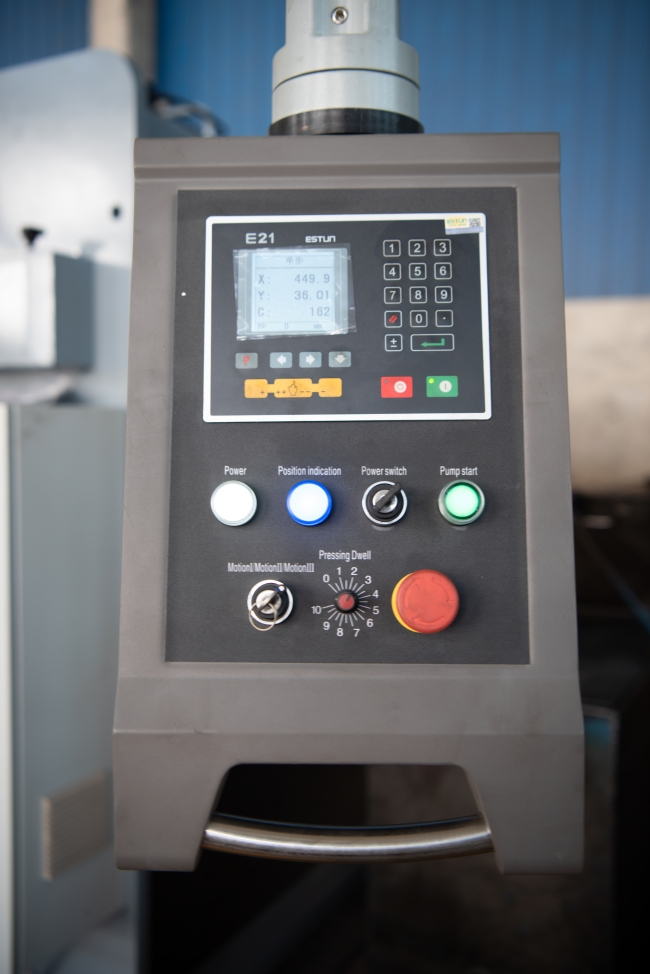
This product is equipped with press brake machine dedicated numerical control device which is applicable to various users. On the basis of ensuring work precision, the cost of numerical control bending machine is reduced significantly.
Features of this product are listed below:
- Positioning control of back gauge.
- Intelligent positioning control.
- Unilateral and bidirectional positioning which eliminates spindle clearance effectively.
- Retract functions.
- Automatic reference searching.
- One-key parameter backup and restore.
- Fast position indexing.
- 40 programs storage space, each program has 25 steps.
- Power-off protection.
CNC Control Systems
CNC press brakes use sophisticated computer systems to automate the entire bending process. These machines are capable of controlling multiple axes simultaneously, including the Y-axis (ram), X-axis (back gauge movement), R-axis (back gauge height), and Z-axis (back gauge lateral movement). Operators can program entire sequences of bends with precise control over each axis, and the machine automatically adjusts between bends without manual intervention.
Key features of CNC control systems include:
- Full Automation:CNC press brakes allow for automatic control of all machine movements, reducing the need for manual intervention.
- Multi-Axis Control:CNC machines control multiple axes, allowing for complex bending operations and increased precision.
- Advanced Programming Capabilities: Operators can use CAD/CAM software to design complex parts and import these designs directly into the CNC press brake. This capability streamlines the production process and reduces setup time.
- Real-Time Monitoring:CNC systems often include real-time feedback systems that monitor the bending process, making automatic adjustments to ensure accuracy.
- Large Program Storage: CNC press brakes can store thousands of programs, making it easy to recall and repeat jobs for consistent, high-volume production.
CNC Controller-ESA-S630 Features
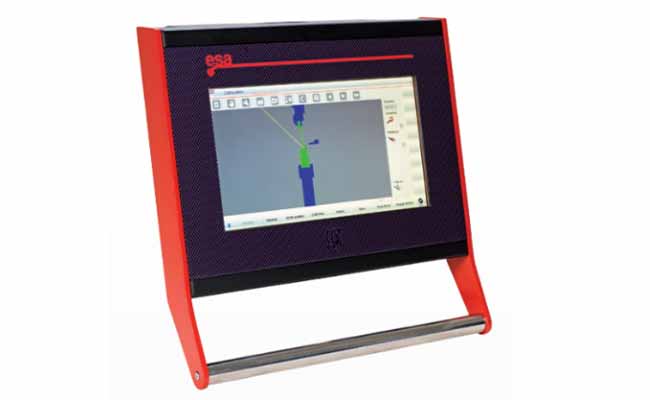
The most powerful in its class. 10” touch screen with powerful graphic.
All the performances of a high-level cnc in an economical and user-friendly controller.
High-level graphic programming for easiness of use and sophisticated algorithms to make the most of your machine.
Direct management of any kind of servo valves with no need of external amplifiers.
Can Manage up to four axes in any combination, including Electrical press brakes and Tandem.
TYPICAL APPLICATIONS
Conventional press-brakes (Mechanical and Hydraulic), synchro Hydraulic press-brakes,
Servo controlled hydraulic single cylinder press-brakes, electrically driven press-brakes, tandem press-brakes
Hydro-mechanical press-brakes American style.
Guillotine shears, with 3-4 axes.
Basic unit equipped with cpu amd etx-lx800 500mhz, 128mb dram including:
- Graphic colour 10” touch screen display (1024 x 600 pixels resolution).
- 128 MB silicon disk.
- Interactive 2d graphic editor for work-pieces and tools data entry
- 2D graphic display of machine frame, work-piece and tools
- Manual 2D graphic identification of the best bending sequence(option)
- 4 fast counting circuits for line drive 0-5Vdc differential encoders or npn/push pull.The encoders are powered at 5Vdc (max 200mA per channel).
- 4 analog outputs(±10V) with 13bits + sign resolution.
- 4 digital inputs for the zero micros.
- 4 analog inputs, 12 bits resolution, ranges 0÷10V, 0÷
- 2 general purposes analog outputs, 0÷10V (8 bits resolution).
- 32 digital inputs (24Vdc).
- 32 digital outputs (24Vdc, 0,7A max.) protected against overload and short-circuits.
- 2 serial port rs232.
- 1 Can port with 9 pins subd f connector.
- 1 ethernet port 10/100 Mbit (lan connection)
- 1 VGA port for external monitor connection
- 2 USB (2.0) ports.
- 24Vdc power supply.
NC Press Brakes And CNC Press Brakes Differences In Precision And Accuracy
Secondly, precision is a crucial factor in metal bending, particularly in industries where even minor deviations can result in costly errors or product defects. NC press brakes and CNC press brakes offer different levels of precision based on their control systems and automation features.
NC Press Brake Precision
While NC press brakes can provide accurate bends, their bending precision largely depends on the skill of the operator. Manual adjustments are required between each bend, which increases the likelihood of small variations in accuracy. For simple or low-precision bending tasks, NC press brakes are more than adequate, but they may struggle to meet the high tolerances required for complex or high-specification parts.
- Operator Dependency:The quality of the bends is largely influenced by the operator’s expertise and manual inputs.
- Manual Adjustments:Because manual adjustments are needed between bends, there is a greater potential for human error.
- Limited Feedback:NC systems lack the advanced sensors and real-time feedback found in CNC systems, making it harder to ensure consistent accuracy.
CNC Press Brake Precision
CNC press brakes excel in precision and repeatability. The computerized control system automatically adjusts the machine’s settings to ensure each bend is performed to the exact specifications. CNC press brakes often include features like angle measurement sensors and automated tool alignment, further enhancing precision.
- High Precision:CNC press brakes achieve high precision thanks to their ability to control multiple axes with extreme accuracy.
- Real-Time Adjustments:Advanced feedback systems allow the machine to make real-time adjustments to maintain consistent accuracy throughout the production run.
- Repeatability:CNC systems are ideal for high-volume production runs that require consistent quality, as they can store and recall programs for repetitive tasks.
NC Press Brakes And CNC Press Brakes Differences In Speed and Efficiency
Thirdly, speed and efficiency are vital in any manufacturing process, particularly for businesses that need to meet tight production schedules. The automation level of a press brake directly impacts its speed and overall productivity.
NC Press Brake Bending Speed
NC press brakes require more manual input and adjustments between bends, which can slow down the production process. Each bend must be programmed individually, and operators must manually reset the machine for the next operation. While NC press brakes are still relatively fast for simple tasks, their efficiency decreases when handling complex parts or high-volume production.
- Manual Adjustments Slow Down Process:Manual adjustments between bends can reduce overall production speed.
- Suitable for Low to Medium Production Runs:NC press brakes are generally more efficient for smaller production runs or simpler bending tasks.
CNC Press Brake Speed
CNC press brakes are significantly faster and more efficient than NC models due to their automation and advanced control systems. Once a program is created, the CNC press brake can execute multiple bends in rapid succession without manual intervention. The machine can automatically adjust the back gauge, ram, and other components for each new bend, minimizing downtime between operations.
- Automation Increases Speed:The full automation of CNC press brakes allows for faster bending operations, especially in high-volume production environments.
- Quick Setup and Tool Changes:CNC press brakes feature automatic tool changes and adjustments, further reducing downtime and improving efficiency.
- Ideal for High-Volume Production:CNC press brakes excel in large-scale production runs, where speed and efficiency are crucial.
Programming and Interface Complexity
Fourthly, both NC press brakes and CNC press brakes require programming, but the complexity and capabilities of the programming interfaces differ significantly between the two types.
NC Press Brake Programming
NC press brake machine typically have a simpler, more basic programming interface. Operators must input numerical data manually for each bending operation, including values like bend angle, material thickness, and the position of the back gauge. While some NC press brakes allow operators to store basic programs, their memory capacity is limited, and the programming process can be time-consuming for complex parts.
- Basic Programming Interface:NC systems rely on simple numerical inputs, making them easier to learn but more time-consuming for complex projects.
- Limited Program Storage:NC press brakes have limited storage for bend programs, meaning operators may need to re-enter data for different jobs.
CNC Press Brake Programming
CNC press brake feature a far more advanced programming interface, often including graphical displays, 3D simulations, and touchscreens. Operators can design parts using CAD/CAM software and import these designs directly into the CNC press brake. The machine’s computer system can then generate the appropriate bending sequences, automatically adjusting for factors like material type, thickness, and bend radius.
- Advanced Programming Capabilities:CNC press brakes offer advanced programming features, allowing operators to import complex designs and automate the entire bending process.
- 3D Simulation and Visualization:CNC systems often include 3D simulation tools that allow operators to visualize the bending process before starting production, reducing errors and waste.
- Large Program Storage Capacity:CNC press brakes can store thousands of programs, making it easy to recall previous jobs and repeat them with precision.
Flexibility and Complexity of Operations
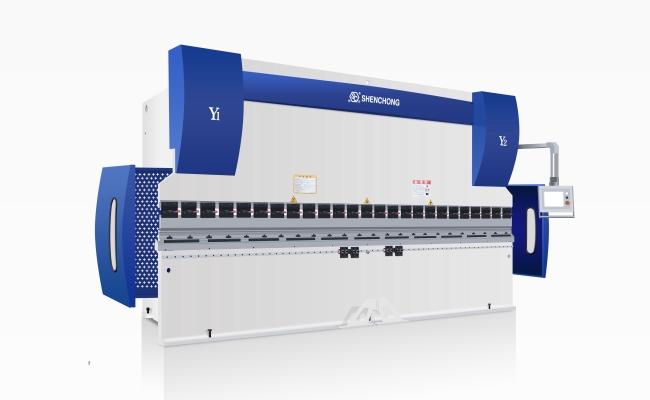
Fifthly, the flexibility of a press brake refers to its ability to handle various materials, thicknesses, and complex bending operations. Both NC and CNC press brakes can be used for a wide range of applications, but CNC press brakes are far more versatile.
NC Press Brake Flexibility
NC press brakes are suitable for basic bending tasks and can handle a variety of materials, including steel, aluminum, and stainless steel. However, their flexibility is limited by the need for manual adjustments between bends. NC press brakes are better suited for simpler parts with fewer bends and less demanding specifications.
- Good for Basic Tasks:NC press brakes are ideal for simpler bending tasks that don’t require high levels of precision or complex bend sequences.
- Limited Material Flexibility:NC press brakes can work with different materials, but changing materials or thicknesses may require additional setup and manual adjustments.
CNC Press Brake Flexibility
CNC press brakes offer superior flexibility, capable of handling complex parts, multiple materials, and varying thicknesses with ease. The ability to control multiple axes and automate tool changes allows CNC press brakes to perform intricate bends and switch between different materials quickly. This makes them ideal for industries that require a high degree of customization and frequent job changes.
- High Complexity Handling:CNC press brakes excel at producing parts with complex geometries, tight tolerances, and varied angles.
- Easy Material and Thickness Changes:CNC systems can adjust for different materials and thicknesses without the need for manual intervention, reducing setup time and improving efficiency.
- Versatility in Applications:CNC press brakes are suitable for a wide range of industries, including aerospace, automotive, electronics, and construction, where precision and flexibility are essential.
Cost and Investment Considerations
Need to be mentioned, cost is a significant factor when choosing between NC and CNC press brakes, as these machines represent a major investment for any fabrication shop or manufacturing facility.
NC Press Brake Cost
NC press brakes are generally less expensive than CNC models, making them a more affordable option for smaller workshops or manufacturers with simpler production needs. The lower cost reflects the reduced automation capabilities and simpler control system. While NC press brakes offer a good balance of functionality and cost, they may not provide the long-term value that CNC machines offer in terms of efficiency and productivity.
- Lower Initial Investment:NC press brakes are more affordable upfront, making them an attractive option for small businesses or operations with limited budgets.
- Lower Operating Costs:NC press brakes tend to have lower maintenance and operating costs compared to CNC machines, though they may require more manual labor.
CNC Press Brake Cost
CNC press brakes are more expensive due to their advanced technology, multi-axis control systems, and automation features. However, the higher initial investment is often justified by increased productivity, precision, and reduced labor costs over time. For manufacturers that require high-volume production, complex bending operations, or consistent quality, CNC press brakes offer superior long-term value.
- Higher Initial Investment:CNC press brakes require a larger upfront investment, but this cost is often offset by the machine’s ability to improve productivity and reduce waste.
- Lower Labor Costs:CNC machines require less manual labor, reducing the need for highly skilled operators and lowering long-term labor costs.
- Long-Term Value:CNC press brakes offer better long-term value for companies that prioritize efficiency, precision, and scalability.
NC Press Brakes And CNC Press Brakes Differences In Applications and Industries
Last but not least, both NC and CNC press brakes are used in a variety of industries, but their suitability depends on the complexity and scale of the application.
NC Press Brake Applications
NC press brakes are suitable for small to medium-sized production runs and simpler bending tasks. They are commonly used in industries that require basic metal fabrication, such as construction, HVAC, and light manufacturing. NC press brakes are ideal for businesses that produce less complex parts with fewer bends and lower precision requirements.
- Construction: NC press brakes are often used in the construction industry for bending basic metal components, such as brackets, supports, and framing elements.
- HVAC: The HVAC industry uses NC press brakes for bending sheet metal to create ducts, vents, and other ventilation components.
- Light Manufacturing: NC press brakes are suitable for small workshops and manufacturers that produce simple metal parts with moderate precision requirements.
CNC Press Brake Applications
CNC press brakes are widely used in industries that require high precision, complex geometries, and large production volumes. These industries include aerospace, automotive, electronics, and heavy manufacturing, where accuracy and repeatability are critical. CNC press brakes are ideal for businesses that need to produce customized parts, handle a variety of materials, and achieve consistent quality across large production runs.
- Aerospace:The aerospace industry requires high-precision metal components with tight tolerances, making CNC press brakes the ideal choice for fabricating aircraft parts.
- Automotive:CNC press brakes are used in the automotive industry to produce complex metal parts, such as body panels, chassis components, and brackets.
- Electronics:In the electronics industry, CNC press brakes are used to bend sheet metal for enclosures, housings, and other precision components.
- Heavy Manufacturing:CNC press brakes are suitable for large-scale manufacturing operations that produce high volumes of complex, precision-demanding parts.
Conclusion
In summary, both NC and CNC press brakes offer distinct advantages, and the choice between the two depends on your specific production needs, budget, and operational requirements.
- NC press brakes are ideal for smaller workshops or manufacturers that handle simple bending tasks and require a more affordable solution. They offer basic automation capabilities, but manual intervention is needed between bends, and precision is largely dependent on the operator’s skill.
- CNC press brakes, on the other hand, are designed for high-precision, high-volume production environments where speed, accuracy, and automation are critical. CNC machines offer superior control over multiple axes, advanced programming capabilities, and the ability to handle complex parts and materials with minimal manual input.
Ultimately, businesses that prioritize precision, flexibility, and efficiency will benefit most from investing in a CNC press brake, while those with simpler needs may find that an NC press brake provides the functionality they require at a lower cost. By understanding the differences between these two types of machines, manufacturers can make informed decisions that optimize their production processes, reduce costs, and improve overall productivity.