In industrial settings, the need for effective surface preparation is paramount. Two commonly used technologies for surface treatment are metal deburring machines and laser cleaning machines. While both aim to enhance the surface quality of metal components, they employ different methods and technologies. This article provides a comprehensive comparison of metal deburring machines and laser cleaning machine, discussing their functions, specifications, advantages, disadvantages, applications, and future trends.
Understanding Metal Deburring Machines
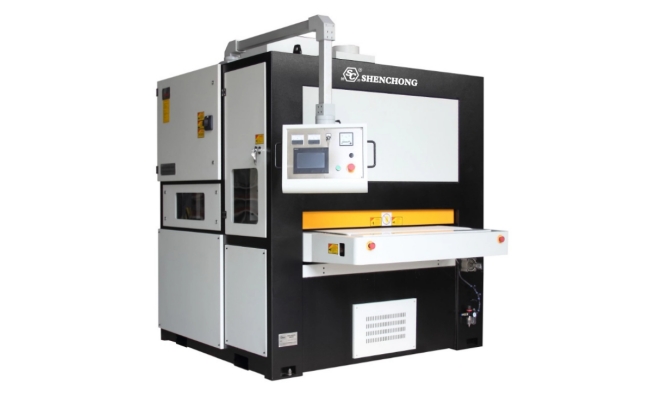
Metal Deburring Machines Definition and Purpose
Metal deburring machines are specialized equipment designed to remove burrs, sharp edges, and imperfections from machined or cast metal components. Burrs are unwanted protrusions that can affect the performance, aesthetics, and safety of parts. The primary purpose of deburring is to ensure a smooth surface finish, which is critical for subsequent processes such as coating, assembly, and final inspection.
Types Of Metal Deburring Machines
Metal deburring machines can be categorized into several types:
- Mechanical Metal Deburring Machines:Use mechanical tools such as brushes, grinding wheels, or abrasives to remove burrs. Examples include vibratory deburring machines and barrel finishing machines.
- Chemical Metal Deburring Machines:Utilize chemical solutions to dissolve burrs and improve surface finish. This method is often used for complex geometries.
- ThermalMetal Deburring Machines: Employ heat to remove burrs by melting them away. This process is effective for hard-to-reach areas.
Metal Deburring Machines Technical Specifications
Key technical specifications for metal deburring machines often include:
- Speed:The rate of processing, often measured in parts per hour.
- Power Consumption:Energy usage, typically measured in kilowatts.
- Capacity:Maximum part size and weight the machine can accommodate.
- Type of Abrasive:The kind of abrasive material used in the process.
- Automation Level: Manual, semi-automatic, or fully automated systems.
Understanding Laser Cleaning Machines
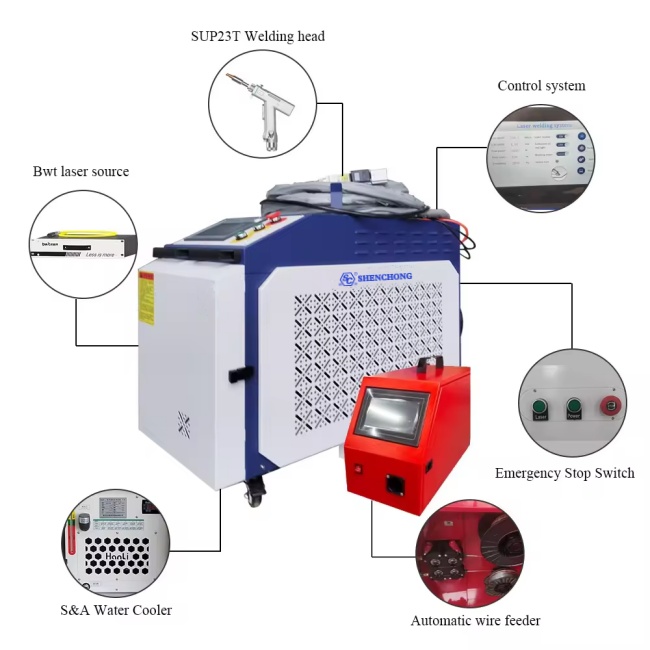
Laser Cleaning Machines Definition and Purpose
Laser cleaning machines use high-energy laser beams to remove contaminants, rust, and other unwanted materials from metal surfaces. This method is highly effective for cleaning delicate components without causing damage. The purpose of laser cleaning is to restore the original surface condition of parts, preparing them for further processing or use.
Types of Laser Cleaning Systems
Laser cleaning systems can be classified into several categories based on their design and application:
- Fiber Laser Cleaning Machines:Use fiber laser technology for efficient and precise cleaning. They are compact and suitable for a wide range of applications.
- CO2 Laser Cleaning Machines:Utilize CO2 lasers for effective removal of organic materials, such as paint and coatings.
- Pulsed Laser Cleaning Systems:Provide high-energy pulses for cleaning tough contaminants from surfaces.
Laser Cleaning Machines Technical Specifications
Important technical specifications for laser cleaning machines include:
- Laser Power:Typically ranges from 100 W to several kW, affecting cleaning speed and efficiency.
- Pulse Frequency:Determines the number of laser pulses per second, impacting the cleaning process.
- Cleaning Speed:Measured in square meters per hour, indicating how quickly surfaces can be cleaned.
- Weight and Dimensions:Influences installation and operational flexibility.
Advantages and Disadvantages
Metal Deburring Machines Advantages and Disadvantages
Advantages:
- Effective Removal:Mechanical deburring machines can efficiently remove burrs and achieve a smooth finish.
- Variety of Methods:Multiple deburring methods allow for tailored solutions based on part geometry.
- Cost-Effective:Often less expensive compared to laser cleaning machines in terms of initial investment.
Disadvantages:
- Material Removal:Some methods may remove more material than desired, affecting part dimensions.
- Surface Damage Risk:Mechanical processes can inadvertently damage delicate surfaces.
- Higher Maintenance:Mechanical components may require regular maintenance and replacement.
Laser Cleaning Machines Advantages and Disadvantages
Advantages:
- Precision:Laser cleaning is highly precise, minimizing the risk of damaging the underlying material.
- Environmentally Friendly:Generally uses fewer chemicals and produces less waste compared to chemical methods.
- Versatile:Effective for a wide range of contaminants and materials, including rust, paint, and oils.
Disadvantages:
- Initial Cost:Higher upfront investment compared to mechanical deburring machines.
- Operator Skill Requirement:Requires trained personnel for optimal operation and safety.
- Limited Thickness Capability:Not as effective for heavy contaminants or thick layers of material.
Applications In Industry
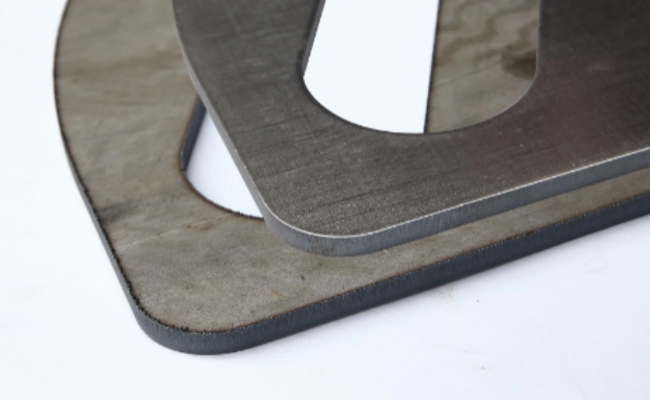
Metal Deburring Machines Applications
- Automotive Manufacturing:Used to deburr engine components, gears, and other critical parts.
- Aerospace Industry:Essential for ensuring the quality of components subjected to high stress and fatigue.
- General Manufacturing:Widely utilized in production lines for various metal products.
Laser Cleaning Machines Applications
- Art Restoration:Used to clean intricate sculptures and historical artifacts without damage.
- Oil and Gas Industry:Effective in removing rust and contaminants from pipelines and equipment.
- Construction:Cleaning metal surfaces before welding or painting to ensure optimal adhesion.
Comparison Of Metal Deburring Machines And Laser Cleaning Machine Cost Considerations
When comparing costs, it’s essential to consider both initial investment and long-term operational costs.
Initial Costs
- Metal Deburring Machines:Generally less expensive than laser cleaning machines, with costs ranging from a few thousand to tens of thousands of dollars depending on the type and complexity.
- Laser Cleaning Machines:Higher initial investment, often starting from $20,000 and going up significantly for more advanced models.
Operating Costs
- Metal Deburring Machines:Operating costs may include abrasive materials, maintenance, and energy consumption.
- Laser Cleaning Machines:Typically lower operating costs, primarily involving energy consumption and minimal consumables.
Maintenance Costs
Metal Deburring Machines Maintenance Costs
Regular maintenance is necessary to ensure optimal performance. This includes:
- Checking and replacing abrasive materials.
- Lubricating moving parts.
- Ensuring proper calibration for consistent results.
Laser Cleaning Machines Maintenance Costs
Maintenance requirements for laser cleaning machines are generally lower, but include:
- Regular inspection of laser components.
- Cleaning of optics to ensure efficiency.
- Software updates for automated systems.
Cost Aspect | Metal Deburring Machines | Laser Cleaning Machines |
Initial Purchase Cost | Typically ranges from $5,000 to $50,000+ | Usually ranges from $20,000 to $100,000+ |
Operating Costs | Moderate; includes abrasives, maintenance, and energy consumption | Generally lower; mainly energy and minimal consumables |
Maintenance Costs | Regular maintenance required for mechanical parts; costs can vary based on machine type | Lower maintenance; requires periodic checks on laser components |
Labor Costs | May require skilled operators, but automation can reduce labor costs | Requires trained personnel for operation, but automation is increasingly common |
Consumable Costs | Costs for abrasives, brushes, and other materials can add up over time | Minimal; mainly focused on energy costs with less frequent replacements needed |
Return on Investment (ROI) | Can be quick due to increased efficiency and reduced labor costs | Higher initial investment, but potentially high ROI due to efficiency in cleaning and reduced waste |
Notes:
- Initial Purchase Costcan vary significantly based on the machine’s size, capacity, and capabilities.
- Operating Costsdepend on the volume of production and the specific processes used.
- Maintenance Costsmay increase with more complex machines or those used in high-demand environments.
- Labor Costsare influenced by the level of automation and the skill set required for operation.
- Consumable Costsrefer to any materials or items that need to be replaced regularly during operation.
This table provides a clear comparison of the cost considerations associated with metal deburring machines and laser cleaning machines, helping you assess which option may be more suitable for your specific needs.
Future Trends in Deburring and Cleaning Technologies
The landscape of metal surface treatment technologies is continuously evolving. Key trends include:
- Automation:Increasing integration of robotics in both deburring and laser cleaning processes for enhanced efficiency.
- Eco-Friendly Practices:A shift towards environmentally friendly materials and methods in surface preparation.
- Digitalization:The adoption of IoT and AI for monitoring and optimizing performance in real-time.
Conclusion
Both metal deburring machines and laser cleaning machines serve crucial roles in enhancing the surface quality of metal components, but they employ fundamentally different methods. Deburring machines are effective for removing sharp edges and imperfections, while laser cleaning machines excel in precision cleaning without damaging the underlying material. The choice between the two depends on specific application requirements, budget, and desired outcomes. Understanding these differences will help manufacturers make informed decisions that enhance productivity and product quality.