Table of Contents
Panel benders are advanced machines designed for high-precision metal sheet bending, commonly used in industries that require automated and efficient processing of large quantities of metal panels. They are known for their flexibility and capability to handle complex bending jobs with minimal manual intervention. This article will provide an overview of the panel bender operation process and important considerations to ensure safe and optimal performance.
Overview Of Panel Bender Operation
Panel benders are highly automated, with a system that positions the sheet, clamps it, and performs bends through a programmable series of movements. Operators need to follow specific steps for successful operation:
Step-by-Step Process:
Material Preparation
- Sheet Inspection: Before starting, ensure the metal sheets meet the size, thickness, and material specifications of the job.
- Handling and Loading: Carefully load the sheet onto the machine. Some panel benders have automatic loading systems, but manual systems may require operators to position the sheet accurately on the worktable.
Setting The Program
- Program Selection: Use the machine’s CNC (Computer Numerical Control) interface to select the appropriate bending program. The program will dictate the bending sequence, angles, and dimensions according to the design.
- Parameter Input: Ensure all parameters like sheet thickness, bending radius, and angles are entered correctly into the system. Fine adjustments may be necessary depending on the material properties.
Test Running
- Trial Bend: Before running the full production, it’s essential to do a trial bend with a test sheet. This ensures that the programmed settings produce the correct angles and dimensions.
- Adjustments: If there are discrepancies in the trial, adjust the program or machine settings accordingly.
Bending Process
- Automated Bending: Once everything is set, the machine will automatically feed and position the sheet, perform the bend sequences, and produce the desired shapes. The operator’s role here is primarily to monitor the process.
- Quality Control: During the bending process, periodically check the bent parts for accuracy. This helps catch any issues early before producing a large batch.
Finishing Steps
- Unloading: Once the parts are bent, they can be manually or automatically unloaded from the machine.
- Post-Processing: In some cases, further processing like deburring or additional forming may be required before the parts are ready for assembly or shipment.
Key Considerations For Panel Bender Operation
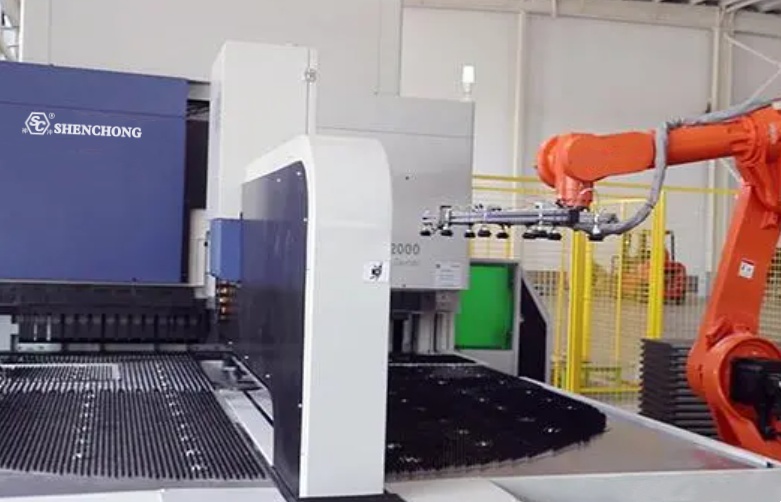
Material Specifications
Different materials (e.g., steel, aluminum, copper) require specific bending settings, as the properties like ductility, strength, and thickness can affect the final product. Always verify the material is suitable for the programmed job.
Machine Setup And Maintenance
Proper setup of the machine is critical to ensure accurate and consistent bending results. Make sure to regularly check for wear and tear on critical components such as clamping systems, blades, and forming tools.
Lubrication and Cleaning: Ensure that all moving parts are adequately lubricated, and the machine is clean to prevent errors during operation.
Program Accuracy
The CNC program must be correctly calibrated for each job, as inaccurate settings can result in poor-quality bends. Minor variations in material thickness or machine setup can greatly influence the outcome, so it’s important to fine-tune each job.
Safety Measures
- Personal Protective Equipment (PPE): Operators should always wear appropriate safety gear, including gloves, goggles, and protective clothing, to avoid injuries from sharp metal edges or machine operation.
- Emergency Stops: Always be aware of the emergency stop functions and ensure that safety guards are in place during operation. Never reach into the machine while it is running.
- Machine Maintenance: Regular maintenance and servicing are key to ensuring safe operation. Check the system regularly for any mechanical issues or software glitches.
Precision And Quality Control
Continuous monitoring and frequent quality control checks are crucial to ensure that each bent panel meets the design specifications. Automatic or manual measurements of angles and dimensions should be performed throughout the production run.
Advanced Features In Panel Benders
Many panel benders come equipped with advanced features to enhance productivity and quality. Some of these include:
- Automated Sheet Loading: Reduces manual handling and increases efficiency by feeding sheets directly into the bending zone.
- Multiple Axis Control: Provides greater flexibility in bending complex shapes and performing multiple bends in different directions.
- Offline Programming: Enables operators to create and simulate bending programs before running them on the machine, reducing setup times and potential errors.
Common Issues And Troubleshooting
- Bend Inaccuracy: If the bends are off, it may be due to incorrect program settings, material inconsistencies, or mechanical misalignment. Recheck the program and ensure that the machine is properly calibrated.
- Material Slippage: If the material is not clamping securely, check the clamping force settings and ensure the sheet is properly positioned on the worktable.
- Surface Damage: If the metal surface is scratched or damaged during the process, check the cleanliness of the machine’s contact points and ensure that no debris is trapped between the sheet and the bending tools.
Efficient Panel Bender Operation
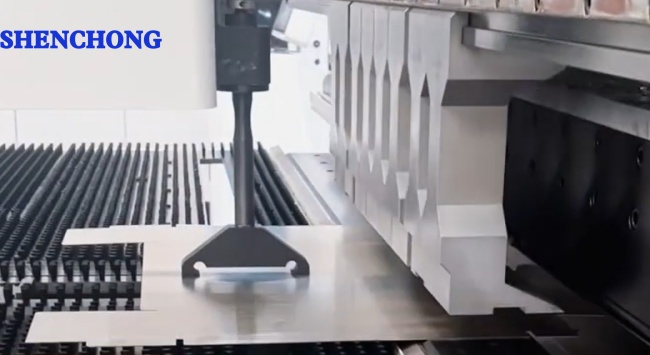
The operation of the panel bending machine plays a crucial role in the manufacturing process. The operational efficiency not only accelerates the production speed, but also ensures the quality of the final product. This includes regular maintenance of the machine, appropriate training for operators, and the use of technology to simplify operations. The advanced panel bender machine is equipped with software that can pre program the bending sequence, automatically adjust bending parameters based on material data, and even simulate the bending process to identify potential problems before they occur.
Combining these design considerations from the beginning can significantly improve the efficiency and quality of the panel bending process. By understanding and applying the principles of bending allowance, designing to minimize waste, and effectively operating panel bending machines, manufacturers can ensure that their projects are not only successful, but also sustainable and cost-effective.
Set Up The Machine: Calibration And Material Settings
The initial setting of the panel bender machine is a key step that directly affects the efficiency, accuracy, and quality of the bending process. Correct calibration and material settings, as well as careful tool selection and configuration, are crucial for ensuring optimal performance. Let’s explore the key considerations and steps involved in setting up a machine for operation.
Calibration And Material Settings
Calibration is the process of configuring a machine to accurately execute according to the specifications of the materials used. This includes adjusting machine settings such as bending angle, force, and post gauge position to match the thickness, type, and other characteristics of the material. Accurate calibration is crucial for compensating for any differences in material properties and ensuring that each bend is consistent and precise.
The material setting also plays an important role in the preparation stage. This includes loading metal plates onto the machine and ensuring their correct positioning. Alignment of materials is crucial for achieving the desired results before the bending process begins, as even slight misalignment can lead to defects in the final product.
Panel Bender Operation: Tool Selection And Configuration
Choosing the appropriate tool for the panel bending machine is another key aspect of the setup process. The selection of tools, such as curved blades and clamping rods, should be based on the specific requirements of the bending task, including material type, thickness, and bending geometry. Each tool has its own specifications and capacity, and using the wrong tool may result in poor bending quality or damage to the machine.
The configuration of the tool includes adjusting settings to align with the material and desired bending. This may include setting the correct blade clearance, adjusting clamping force, and configuring post gauge to achieve precise material positioning. The correct configuration ensures efficient machine operation and minimizes the risk of errors or waste.
In short, the setup of the automatic panel bending machine is a fundamental step that requires careful attention to calibration, material settings, and tool selection. By carefully configuring machines to meet specific material and project requirements, manufacturers can achieve high-quality bending with optimal efficiency. This preparation not only improves the performance of the machine, but also contributes to the overall success and profitability of the manufacturing process.
Bending Process Technology: Sequential Bending Steps Operation
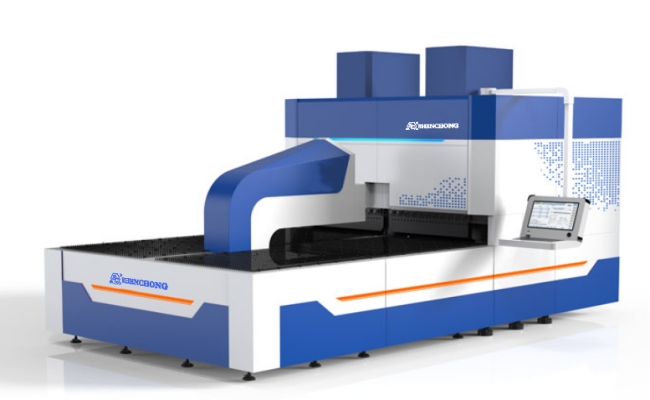
Mastering the bending process requires not only understanding how to operate the machine. This is about understanding the best techniques for handling various projects, especially when dealing with sequential bending operations and complex shapes and angles. These technologies are crucial for ensuring efficient production of high-quality and precise components. Let’s delve into the strategies and precautions for successful bending processes.
Sequential Bending Operation
Sequential bending is a technique of performing multiple bends in a specific order to create the desired part. This method requires careful planning to ensure that each bend does not interfere or hinder subsequent bends. The main considerations include:
Plan the bending sequence to minimize material movement and reduce the risk of collision with machine parts.
Adjust the bending force and post gauge position of each step to adapt to the constantly changing geometric shape of the parts.
Before actual production, use specialized software to simulate the bending sequence, identify potential issues, and optimize the process.
Handling Complex Shapes And Angles
The complex shapes and angles present unique challenges during the bending process. Technologies for managing these complexities include:
- By utilizing advanced tools, it is possible to adapt to complex bends and shapes, ensuring accuracy and quality.
- Implement incremental bending technology to create complex angles or curves, which can better control the bending profile.
- Using 3D modeling and simulation tools to plan and visualize the bending process, ensuring the accuracy of complex parts.
In short, the success of the bending process depends on a deep understanding of continuous bending operations and the ability to accurately handle complex shapes and angles. By applying these technologies, manufacturers can tackle the challenges posed by complex designs and ensure that every project is completed to the highest standards. This professional level not only improves the performance of the panel bending machine, but also greatly enhances the efficiency and quality of the manufacturing process.
Advanced Technology And Techniques: Precise Bending
Mastering advanced techniques and skills is crucial to elevate the art of panel bending to its peak. Achieving high precision and consistency, handling rebound, and optimizing speed are all professional knowledge that distinguish excellent manufacturers from excellent manufacturers. Let’s delve into these advanced technologies and uncover techniques that can alter the bending process.
Technologies For Achieving High Precision And Consistency
The accuracy and consistency of bending are crucial for high-quality manufacturing. Here are the technologies to achieve these goals:
- Utilize software with advanced algorithms to calculate accurate bending allowances and compensate for material differences.
- Adopt precision fixtures that meet specific material and design requirements to ensure consistent bending every time.
- Implement strict calibration procedures to maintain the accuracy of the machine over time and promptly resolve any deviations.
Dealing With Springback In Sheet Metal Bending
Springback – the tendency of metal to partially return to its original state after bending – may be a major challenge. Combination rebound includes:
- Understand the material properties and how they affect springback, in order to make adjustments for compensation during the bending process.
- Using excessive bending techniques, where the bending angle is slightly greater than the required angle to consider springback.
- Test different tool choices and bending speeds to minimize the impact of springbackon the final product.
Speed Optimization
Improving the speed of the bending process without compromising quality requires optimizing the workflow. This includes:
- Simplify the setup process by using preset programs for quick tool changes and common tasks.
- Optimize the operation sequence, reduce machine downtime and material handling.
- Utilize automation as much as possible to maintain continuous workflows and reduce manual intervention.
Machine Maintenance To Improve Efficiency
Regular active maintenance of the sheet bending machine is crucial for maintaining its efficiency and extending its service life. Key maintenance techniques include:
- Adhere to regular maintenance plans, including inspecting and lubricating moving parts to prevent wear and tear.
- Regularly calibrate the machine to ensure it operates at the highest accuracy.
- Train operators to identify and resolve minor issues before they escalate into costly repairs.
By integrating these advanced technologies and cutting-edge techniques into panel bending processes, manufacturers can achieve unparalleled levels of precision, efficiency, and quality. These practices not only improved the capabilities of panel bending machines, but also made significant contributions to the overall success and profitability of manufacturing operations.
Conclusion
Panel bender operation requires a combination of technical knowledge and attention to detail. By following the correct procedures, maintaining the machine, and ensuring safety precautions, operators can achieve high-quality, consistent results. With advancements in automation and precision, panel benders continue to be an essential tool for efficient metal fabrication in industries worldwide.