Currently, intelligent and flexible processing technology has become the pursuit and aspiration of high-end sheet metal processing manufacturers. Therefore, robot bending units have emerged in this market environment.
Table of Contents
Analysis Of The Current Situation Of Sheet Metal Bending Technology
In the sheet metal industry, most companies are currently engaged in traditional bending processes. In the production process, due to the variety, specifications, and small batch of products, multiple hydraulic press brake machines and a large number of skilled and experienced sheet metal bending operators are still needed to complete the bending of workpieces.
However, in practical work, there are the following problems:
- Firstly, due to the operator working for a long time, the endurance is not sustained, resulting in inconsistent high and low positions of the workpiece placed each time.
- Secondly, operators do not maintain stability like robots, so the size and bending accuracy of the bent workpiece cannot be guaranteed due to manual influence, resulting in poor quality of the finished product.
- Thirdly, when facing large workpieces, it generally requires 3-4 operators to complete the handling and operation, and the difficulty in recruiting workers and high costs are the difficulties faced by enterprises.
- Fourthly, it is not safe for the operatorsto work follow the traditional bending process. There are significant safety hazards when lifting workpieces, which can easily lead to work-related accidents.
Nowadays, although the manufacturing and accuracy of press brake have greatly improved compared to the past, there is still a significant gap between the current requirements and intelligent manufacturing.
In terms of intelligent production, personalized customization, service-oriented extension, and networked collaboration, there is still a need for joint innovation and development in the sub field of sheet metal equipment manufacturing and demand side. This innovation and promotion of application is another improvement and liberation of productivity.
Problems Need To Be Solved In Traditional Sheet Metal Bending Industry
The traditional bending in the sheet metal industry needs to address the following issues:
- Traditional bending process is inability to achieve multi variety, small batch, and fast switching.
- The high-precision bending of workpieces in the sheet metal industry has low precision and unstable quality.
- Sheet metal bending operators are scarce, and the labor intensity of workers is high.
- Personnel costs, safety hazards, process layout, management and operation.
The above problems can be solved by selecting intelligent robot bending units, which include: CNC press brake machine, 6-axis robot and 7-axis guide rail, feeding station, magnetic plate separation device, pre alignment positioning workbench, plate flipping mechanism, feeding gripper, finished product stacking, mold library, offline programming software, parametric programming software, secondary development bending software, and extension services.
Composition Of Robot Bending Units
The CNC hydraulic press brake with robots as the core execution component is a highly automated equipment combination, which has the advantages of high efficiency, high quality, and high flexibility.
In flexible bending machine units, selecting appropriate components combinations can provide better support for bending efficiency and flexibility. The bending accuracy depends on the accuracy of the press brake machine itself, the positioning accuracy of the bending robot, and the collaborative control between the robot and the bending brake machine.
The difficulty of collaborative control lies in the speed matching between the robot and the press brake machine, as well as the running trajectory of the robot supporting the workpiece. Poor follow-up effect will seriously affect the bending angle forming result and the flatness of the board surface, thereby affecting the quality of the finished product.
As shown below figure, the standard bending processing unit consists of a robot and a CNC hydraulic press brake as the core, with the gripper, loading table, unloading table, positioning worktable, flipping frame, gripper changing device, and various detection sensors as auxiliary components.
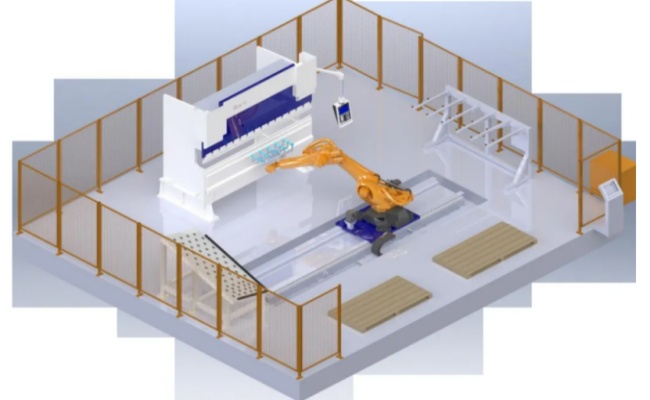
Main Parts of A Robotic Press Brake
Grips are the “hands” used by robots to replace manual labor and pick up and place workpieces. The gripper of a bending robot is usually composed of multiple suction cups installed on a metal frame.
The loading and unloading platforms usually use stacked pallets, and there are also units that use conveyor belts or rollers to transport raw materials and finished products. Oil based boards are prone to adhesion, which can cause multiple boards to be picked up at once. Various splitting devices (such as magnetic splitting devices) and detection sensors can be installed next to the feeding table to ensure that the grabbed boards are single sheets.
The positioning workbench is a tilted platform with a blocking edge, with slightly raised balls distributed on the table surface. The robot transfers the steel plate to the positioning table, and the plate slides freely to the edge due to gravity. Due to the fixed position and edge of the positioning table, when the robot re grasps the board, the position of the board and the gripper are relatively accurately fixed, providing a reference for the next bending step.
The flip frame is a fixed frame for a gripping device. When the robot needs to take the workpiece from a different position, it can place the workpiece on the flip frame to fix it, and then the robot can grab the workpiece in the new position again. In some special occasions, the bending machine mold can also be used to clamp the workpiece and change the gripping position.
Workflow Of Robotic Bending Processing Unit
The bending processing unit work is mainly divided into six processes: loading, picking, centering, flipping, bending, and stacking.
- Loading: Manually place the entire stack of plates that need to be processed on the loading platform, and install a plate detection switch on the loading platform to prevent the robot from grabbing the tray after all the plates are processed.
- Picking: The robot runs to the position of the feeding table and detects the height of the board through the ultrasonic sensor installed on the gripper. Based on the detection data, it automatically runs to the appropriate position for grabbing the board. After grabbing the board, the thickness of the board is measured through a thickness measuring device to avoid processing faults caused by grabbing multiple sheets of board at once. After passing the thickness measurement, it is ready for alignment.
- Centering: The robot runs to the positioning table position, places the sheet metal on the positioning table for precise positioning, and after positioning is completed, grabs the sheet metal again and prepares for bending.
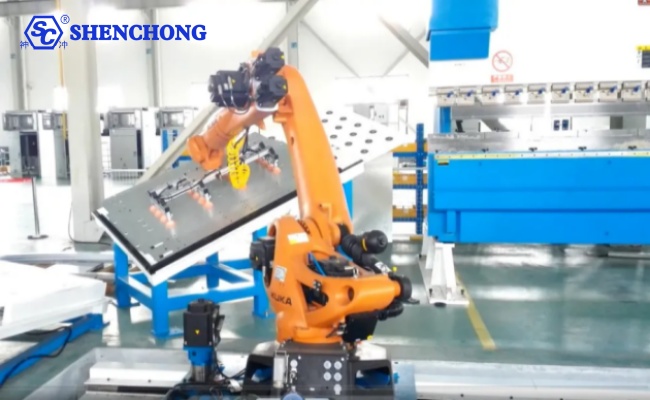
- Flipping: Determine whether to use a flipping frame based on process requirements. If necessary, run the robot to the flipping frame position, place the sheet metal on the flipping frame, release the sheet metal and avoid it. After flipping is completed, grab the sheet metal.
- Bending: The robot runs to the position of the bending machine, flattens the sheet metal onto the lower mold of the bending machine, and accurately locates it through the rear finger sensor of the bending machine. After positioning is completed, the robot sends a bending signal to the CNC press brake and cooperates with the bending machine to complete the bending action to determine whether it needs to be bent again and decide whether to continue bending. Bending is a key link, and the technical difficulty of bending lies in the coordinated action between the robot and the bending machine, that is, bending following. When the robot clamps or supports the bending of the sheet metal, the sheet metal deforms, and the robot needs to follow the sheet metal in a circular arc motion according to a specific trajectory algorithm, and always maintain a relatively fixed position with the sheet metal.
- Stacking: When the robot runs to the position of the unloading table, there are various stacking process actions due to the differences in workpiece forming, such as conventional matrix stacking, single and double layer cross stacking, and forward and reverse interlocking stacking.
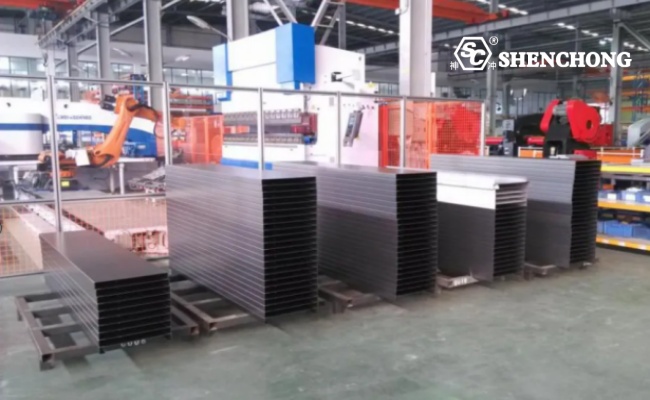
Technical Characteristics Of Robot Bending Units
Design And Development
The research and development of robot bending design focuses on the personalized needs and customization of users, with customer needs and goals as the top priority. Robot bending manufacturers are required to achieve the following before specifying a bending robot solution:
- Conduct detailed technical exchanges with customers in the development of each technical solution
- Perform computer simulation analysis on the workpiece processing drawings provided by the customer
- Conduct on-site sample testing on typical customer workpieces
- Classify and analyze customer workpieces and process data.
After confirming the completion of the above procedural work, the technical plan will be formulated. After the technical plan and plan drawings are approved by the customer, a comprehensive design will be carried out.
SC robotic bending unit adopts advanced 3D design in terms of materials, structure, sensors, real-time compensation, follow-up, laser angle measurement, automatic mold changing, automatic gripper changing, software and control, parametric programming, offline programming, production management software, and bus control technology, all of which adopt and use international first-class brand software and hardware. In terms of the design of the bending machine body, the world’s most advanced design software and methods were used for structural mechanics analysis. With years of design experience and understanding of the structural characteristics of the bending machine frame, finite element analysis was conducted on each force point to achieve mechanical analysis of the side shoulder, upper crossbeam, lower crossbeam, and lower crossbeam of the bending machine, fully ensuring the rationality, reliability, and stability of the machine tool design.
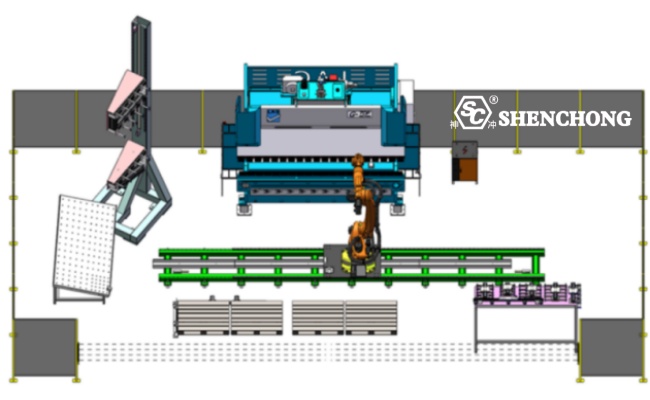
The design of the robot bending unit aims to achieve intelligent product concepts using the latest technologies (software, hardware) for real-time data exchange, compensation, and bending tracking during the production process. The main problems solved and the results achieved are:
(1) Solved the process difficulties of customized sheet metal production, and solved the fast switching production problem of multi product, small batch (5-10 pieces), and multi variety parts in the elevator industry.
(2) Solved the problems of unstable product quality, low precision of parts, and poor product consistency.
(3) Solved the problems of low production efficiency, unreasonable production layout and process route.
(4) Solved the problems of difficult recruitment, high labor costs, and high labor intensity in manual bending.
(5) Improved bending accuracy and automation, enhanced enterprise intelligent manufacturing capabilities, and enhanced the visual effect of customer visits.
Bending Follow-Up Technology
During the bending process, SC robot bending units can automatically follow and adjust workpieces of different sizes and plate thicknesses according to the running speed of the bending brake machine slider. This technology is implemented by the SC SHENCHONG specialized robot bending application software package.
Laser Angle Measurement Technology
The AMS angle measurement system uses a closed-loop laser angle online measurement system. During the automatic bending process of the robot, the automatic application program of AMS and the automatic angle measurement system with built-in laser angle measurement device work together with the SHENCHONG system to ensure the accuracy of the bending angle. Its main characteristics are:
(1) Detecting the bending angle of the workpiece after rebound through laser online.
(2) The force detection system automatically calculates the bending rebound amount.
(3) The depth of the part can be automatically adjusted according to the width of the lower mold.
(4) Through a closed-loop laser angle online measurement system, the bending yield is ensured to reach over 99.5%.
Robot Automatic (ATC) Gripper Changing And Press Brake Tooling Changing
Robot Automatic (ATC) gripper and press brake tooling changing is a fully intelligent and automated operation method in the sheet metal field, which consists of automatic mold changing software, robots, and mold libraries. When equipped with an automatic mold changing system, the precision bending center can automatically and randomly bend small batches of different products. By utilizing the function of automatic mold replacement, the mold in the bending machine is no longer a limiting factor and can be processed by unmanned personnel throughout the entire process. The gripper of the robot’s automatic mechanical device can replace the mold very quickly and can bend the next batch of components at any time.
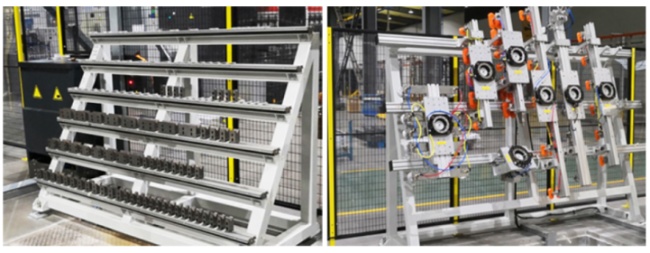
Automatic Press Brake Tooling Changing Software
The main characteristics of automatic mold changing software are:
(1) Through the graphical interface of the attachment, users can immediately see the current status of the entire system. On the right side of the interface, there is a graphic representing the status of the molds, which partitions the current positions of these molds.
(2) The entire interface includes the bending upper punch area, the bending lower die area, and the mold library. The display of the mold follows the size of the mold itself and the position of the clamped workstation.
(3) Distinguish the upper and lower molds with different colors. On the upper left corner of the interface, there is a detailed description of the mold installed on the bending machine. Two parts: one is to explain the upper mold, and the other is to explain the lower mold, describing the clamped mold through identification codes and existing positions.
CNC Sequential Bending Technology
CNC sequential bending technology is a high-precision bending control system suitable for machining workpieces with requirements for shape and positional tolerances. The device consists of a set of two sets of CNC front pushing device operating systems with tracks. The displacement is transmitted and fed back by sensors, and the entire operation is controlled by the CNC system. The control axis is composed of X3 \ X4 and Z3 \ Z4. By configuring a displacement CNC front pushing device and a rear stopper for bending, even if the workpiece size reaches ± 1mm, it can easily ensure that the key dimensions are within controllable errors, improving the accuracy and efficiency of the workpiece.
Software And Control
In the robot bending units, we applied parametric programming software, offline programming software, and production management software. At the same time, we developed secondary bending follow-up, automatic mold changing, automatic gripper changing, flexible stacking, real-time compensation, plate edge searching, flexible flipping technology, and bus control technology. It can greatly meet the technical and software needs of various customers for sheet metal bending.
Robotic Bending Problems And Solutions
When we use robotic press brake for sheet metal bending, we may encounter some small problems that we don’t know how to solve or avoid. Below SC SHENCHONG has compiled five problems that robots are prone to, and provided corresponding solutions.
After Flattening The Long Edge, There Is a Lifting.
Cause analysis: Due to the longer edge that needs to be flattened, it is not tightly pressed during flattening, resulting in the end being flattened and then warped. This situation is closely related to the flattened position, so it is important to pay attention to the flattened position when flattening.
- Before bending, bendthe corner first and then flatten it.
- Step by step flattening: First press the end to bend the flattenedge downwards. Flatten the base.
When Changing The Press Brake Tooling, The Machining Dimensions Will Change.
Cause analysis: Due to the forward squeezing force on the workpiece during the machining process, the workpiece moves forward, resulting in an increase in the small rake angle dimension L at the front.
Solution:
- Grind off the shaded areas in the picture. Usually, we make up as much as there is a difference.
- Grind off all the self positioning parts of the easy mold and use a fixed gauge for positioning.
The Total Size Of The Cutting Material (Referring To Unfolding) Is Too Small Or Too Large, Which Does Not Match The Circular Surface.
Cause analysis:
- Engineering deployment error.
- The cutting size is incorrect.
Solution:
Based on the direction of deviation, the total amount of upward deviation, and the number of bending tools, calculate the allocation for each bend. If the calculated allocation tolerance is within the tolerance range, the workpiece is acceptable.
If the size is too large, small V-grooves can be used for processing.
If the size is too small, a large V-groove can be used for processing.
After The Bending Robot Draws Holes And Engages The Mortise And Tenon, It Expands Or Cracks, Or The Mortise And Tenon Do Not Fit Tightly, Resulting In Deformation.
Cause analysis:
- The reason why the mortise is not tight is due to the inadequate expansion of the hole.
- Deformation is caused by hole misalignment or incorrect mortise and tenon joint method.
Solution:
- Choose a punch with a large R angle and pay attention to the burrs around the hole when pulling and flipping.
- Increase the pressure on the salad hole, deepen it, and use a large R-angle punch instead.
- Change the mortise joint method and the reasons for hole misalignment.
Conclusion
With the overall improvement of the mechanical industry, the sheet metal manufacturing industry will have a new level of requirements for production equipment. In the end, devices that can help users solve problems will be favored by users. SC robot bending unit has a production method suitable for customers, the best combination of hardware and software, and is suitable for customers with multiple varieties, small batches, fast switching, and no need for first piece trial production.