Table of Contents
Hydraulic press ultimate guide will provide you with all the information you need to know about such machines. Hydraulic presses come in various designs and capacities, from small manual models to large industrial machines. They are crucial for tasks such as metal forming, assembly, forging, and even automotive and aircraft manufacturing. Their power and versatility make them invaluable to modern industry and enable them to create and manipulate materials in ways that were previously impossible.
Introduction to a Hydraulic Press
Hydraulic press machine use Pascal’s law to transmit fluid pressure with in different ways. Of course, users can also diversify according to their needs. For example, there are two types of hydraulic presses based on the type of liquid that transmits pressure. The total pressure generated by hydraulic presses is very high and is usually used for forging and stamping. Forging hydraulic presses are divided into forging hydraulic presses and free forging hydraulic presses.
A hydraulic press is a machine that uses hydraulic cylinders to generate compressive force. By using the hydraulic equivalent of a mechanical lever, it expands smaller forces to larger and stronger forces. Yes, it powerful and is the cornerstone of several industries.
Imagine you have a cylinder with a piston inside it. Due to the pressurized hydraulic oil (or some other liquid) pumped into the cylinder, the piston moves up and down.
So, why is this important? Essentially, hydraulic presses are game changers for companies. Whether you are a hydraulic press machine manufacturer or a business owner seeking customized hydraulic press solutions, you cannot overly emphasize the versatility of this machine.
Applications Of A Hydraulic Press Machine
Plastic processing industry: Hydraulic presses are also widely used in the plastic processing industry. Hydraulic presses can be used for opening and closing molds, injection molding, and injection molding processes of plastic products. For example, hydraulic injection molding machines can be used to produce various plastic products, such as bottle caps, toys, household appliance casings, etc. Molded hydraulic press machines can be used to manufacture compression molded products, such as electrical plugs, insulation components, etc. In addition, hydraulic presses can also be used to open and squeeze plastic sheets, such as plastic films, pipes, sheets, etc.
Mechanical processing industry: Hydraulic presses are widely used in the mechanical processing industry and can be used for processing processes such as stamping, bending, die-casting, and stretching. For example, stamping hydraulic presses can be used to manufacture body parts, engine components, and instrument panels for automobiles and motorcycles. Bending hydraulic press can be used for bending metal sheets, such as manufacturing pressure vessels, fan blades, etc. Die casting hydraulic press can be used to cast pressure casting parts, such as automotive engine blocks, automotive components, etc. The stretching hydraulic press can be used for processing metal pipes, metal wire drawing, and other processes.
Hydraulic presses play an important role in the aerospace industry. For example, hydraulic presses can be used for servo control of aircraft components such as landing gear, flaps, and rudder. Hydraulic presses can also be used for the operation and maintenance of aircraft engines and flight control systems. In addition, hydraulic presses can also be used for the manufacturing and assembly of spacecraft, such as servo control and power transmission of spacecraft.
The automotive industry: Hydraulic presses are also widely used in the automotive industry. For example, hydraulic presses can be used in stamping processes in automotive manufacturing, such as stamping of body parts and opening and closing of car door molds. Hydraulic presses can also be used for automotive maintenance work, such as tire replacement, brake system maintenance, etc. Hydraulic presses also play an important role in automotive production lines and can be used for the assembly and assembly of automobiles.
Shipbuilding and marine engineering: Hydraulic presses are widely used in the processing and assembly of large metal components in shipbuilding and marine engineering. The efficiency of hydraulic presses can greatly improve the production efficiency of shipbuilding and marine engineering, while reducing the labor intensity of workers.
Engineering machinery includes excavators, loaders, bulldozers, rollers, etc. The hydraulic system of construction machinery is widely used in various working devices and driving systems, such as steering, braking, transmission, etc. In heavy-duty construction machinery, the application proportion of hydraulic systems is higher, and the working pressure is also greater. The reliability and stability of hydraulic systems are crucial for the operation and safety of construction machinery.
Advantages And Limitations
Advantages Of Using Hydraulic Presses
Hydraulic press has obvious advantages and has become the preferred choice in various industries. Their immense strength is unparalleled, enabling them to easily complete heavy tasks. The precision and control of the hydraulic presses provide are crucial for tasks that require precision, making them essential in fields such as metal processing, automotive, and aerospace.
- Precision and control: Hydraulic presses also excel in precision and control. The ability to precisely adjust pressure and press movement ensures that operations can be carried out with high precisionlevel, which is crucial for the quality and consistency of production.
- High forcecapacity: One of the most prominent advantages of hydraulic presses is that they can generate a large amount of force. This high-strength ability enables them to shape, shape, and cut materials that are difficult or impossible for other types of machinery.
Challenges And Limitations
Although hydraulic presses have many advantages, they also have limitations. They need regular maintenance to maintain effective operation. This includes checking hydraulic oil, seals, and valves, which may be lengthy and require professional skills.
- Maintenance requirements: Regular maintenance is crucial for hydraulic presses. Neglecting maintenance may lead to malfunctions and reduced efficiency, affecting overall productivity and increasing downtime costs.
- Speed and power consumption limitations: Hydraulic presses may be slower than other types of machines, which may be a disadvantage in high-speed production conditions. They can also be energy intensive, especially if they are not properly maintained or used for the most unsuitable applications.
The Core Components Of A Hydraulic Press Machine
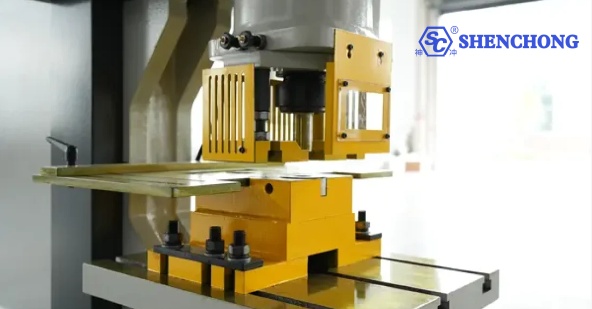
To truly appreciate the strength of a hydraulic press, it is vital to understand its key components. Each part plays a crucial role in ensuring the press operates safely and effectively. Here is a rundown of the essential components that make up a hydraulic press:
It is crucial to understand the key components of a hydraulic press in order to truly understand why it is so powerful. Each part of the hydraulic presses plays a crucial role ensuring the safe and effective operation. The following is an overview of the basic components that make up a hydraulic press:
Hydraulic Cylinder
Hydraulic cylinders are essentially the core of hydraulic presses. Here, hydraulic fluid is pumped out to generate the force that completes the work of the press. The cylinder is composed of pistons that move up and down, applying necessary pressure to the material placed on the press.
Pump
Pump is responsible for moving hydraulic oil to the cylinder. Pumps can be manual, or powered by electric air, or hydraulic driven, and play a crucial role in determining the speed and efficiency of the press.
Pressure Relief Valve
Pressure relief valve ensures that the pressure in the hydraulic system does not exceed the safety limit. It is an important component to prevent overload and potential damage to the press and operator.
Frame
This machine frame of the hydraulic press supports the entire hydraulic system and withstands the forces applied during the compression process. It requires a strong structure to handle with the enormous pressure involved.
Control Panel
The control panel is the brain of a hydraulic press. Here, you can control the settings, adjust the pressure, and basically program the hydraulic press to execute your commands. Modern control panels are typically equipped with touch screen interfaces that can be programmed to automate tasks.
Worktables
Last but not least, we have a worktable. This is where the pressing action occurred. The workbench is specifically designed to handle various materials and sizes. Depending on the nature of the project, you may need a workbench with special features such as temperature control or adjust heights function.
Types Of Hydraulic Press
One of the first things you’ll notice when diving into the world of hydraulic presses is the sheer variety available. Whether you’re a seasoned manufacturer or a hobbyist, choosing the right type of hydraulic press can be pivotal for your project’s success. Let’s take a closer look at some popular types.
When you tend to purchase hydraulic presses, one of the first things you will notice is the types variety. Whether you are an experienced manufacturer or an hobbyist, choosing the right type of hydraulic press is the key to the success of your projects. Let’s take a closer look at some popular hydraulic press types.
C Frame Hydraulic Press
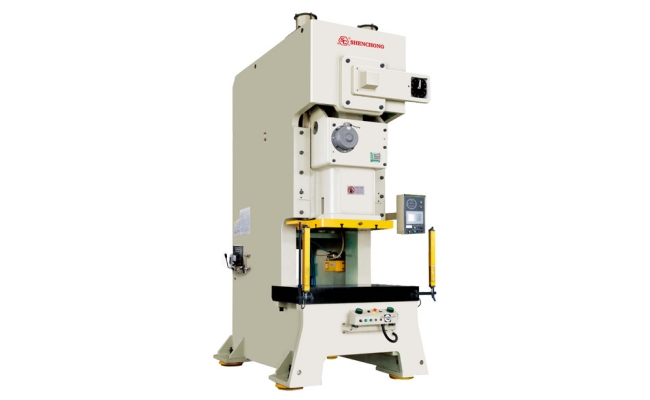
The C Frame hydraulic press gets its name from its C shaped frame, which allows for easier access to the die area. These presses are often used in applications requiring higher precision and are usually electrically operated. They are excellent for assembly, straightening, and other specialized tasks.
Basic Working Principle Of C Frame Hydraulic Press
C type CNC hydraulic press is a mechanical equipment that uses hydraulic transmission and CNC technology control. Through computer program control, the movement of hydraulic presses can be precisely controlled, thereby improving production efficiency and product quality in industrial production.
The Workflow Of C-Type CNC Hydraulic Press
After the operator inputs the processing parameters, the hydraulic press will automatically perform relevant actions, including compression, cutting, forming, and returning of the workpiece. These actions are controlled by the hydraulic system, making the machining process more automated and efficient.
Application Of C-Type CNC Hydraulic Press
C type CNC hydraulic presses are widely used in industries such as metal processing, plastic processing, and rubber processing. For example, in metal processing, it can be used for processes such as stamping, bending, and stretching. In plastic processing, it can be used for operations such as injection molding and extrusion molding.
H Frame Hydraulic Press Machine
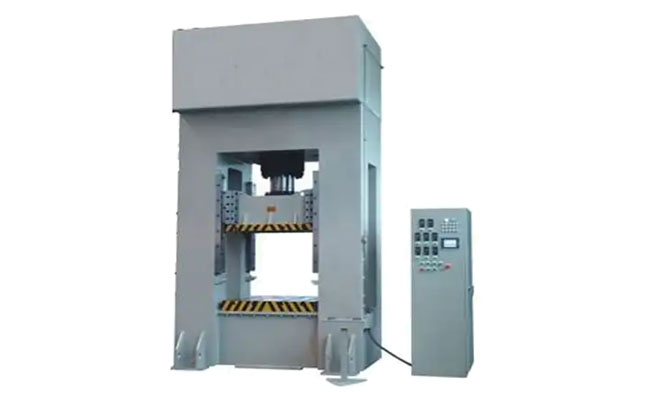
A H-type hydraulic press, also known as a H-frame hydraulic press, is a hydraulic press commonly used in various industrial applications. It is named after its unique H-shaped frame structure. The machine consists of a vertical frame and a horizontal crossbeam located between the vertical sides of the frame, forming the shape of the letter “H”.
H Frame Hydraulic Press Working Principle
The H-frame hydraulic press is a hydraulic press that operates according to the principle of Pascal’s law, which stipulates that when pressure is applied to the fluid in the container, the pressure will be uniformly transmitted in all directions. The following is a breakdown of the working principle of the H-frame hydraulic press:
- Structure: The H-frame hydraulic press is composed of a sturdy H-frame, providing stability and support for the operation of the press. Theframe typically consists of two vertical columns connected by upper horizontal beams, forming an “H” shape.
- Hydraulic system: The hydraulic system of the press includes a hydraulic pump, hydraulic oil, hydraulic cylinder, and control valve. The hydraulic pump is responsible for generating hydraulic pressure by pushing hydraulic oil into the cylinder.
- Hydraulic cylinders: The hydraulic cylindersare located on both sides of the hydraulic press and is connected to the column. They are composed of cylinders, pistons, and piston rods. The piston divides the cylinder into two chambers: the pressure (or power) chamber and the return oil chamber.
- Working cycle: The working cycle of the H-frame hydraulic press usually includes the following steps:
- Loading: Place the workpieceor materials between the plates or molds that connected to the piston rod of the hydraulic cylinder.
- Activation: The operator initiates the press operation by operating the control valves, which direct the flow of hydraulic fluid. The control valves allow the hydraulic fluid to enter the power chamber of the cylinders.
- Pressure application: As the hydraulic fluid enters the power chamber, it exerts pressure on the piston, which, in turn, applies force to the workpiece. The hydraulic pressure is transmitted equally in all directions, allowing for even and controlled pressing.
- Pressing: The hydraulic cylinders continue to exert force on the workpiece until the desired pressure or deformation is achieved. The pressure can be adjusted by regulating the flow of hydraulic fluid or by changing the size of the cylinders.
- Release: Once the pressing operation is complete, the operator releases the pressure by diverting the hydraulic fluid from the power chamber back to the return chamber.
5. Unloading: Then remove the workpiece to be pressed from between the pressure plate or mold, and prepare the hydraulic press for the next cycle.
H-shaped frame hydraulic presses are widely used in various industries, such as forming, bending, straightening, stamping, punching, and other tasks that require high strength and precision. Its sturdy structure and hydraulic power allow for efficient and controllable stamping operations.
Features And Components Of An H-Frame Hydraulic Press Machine
- Frame: The frame of the machine provides stability and support. It is typically made of heavy-duty steel and designed to withstand high-pressure forces.
- Hydraulic system: The hydraulic system powers the press and generates the force required for pressing applications. It includes a hydraulic pump, cylinders, valves, and hoses. Hydraulic fluid is used to transmit the pressure from the pump to the cylinders.
- Cylinder: The hydraulic cylinder is responsible for generating the pressing force. It consists of a piston inside a cylinder that moves under hydraulic pressure. The force applied by the cylinder determines the pressing capacity of the machine.
- Ram or platen: The ram or platen is the movable component of the press that comes in contact with the workpiece. It is attached to the hydraulic cylinder and moves vertically to apply force or perform pressing operations.
- Control system: H-frame hydraulic presses feature a control system that allows operators to control the machine’s functions. It typically includes buttons, switches, or a touchscreen interface for operating the press, controlling the pressure, and adjusting other parameters.
H-frame hydraulic presses are widely used for various applications such as metal forming, forging, stamping, bending, straightening, punching, and assembly operations. The H-frame design offers stability and rigidity, making it suitable for handling heavy workpieces and applying high force. These presses are available in different sizes and configurations to meet specific industrial requirements.
Four-Column Hydraulic Press Machine
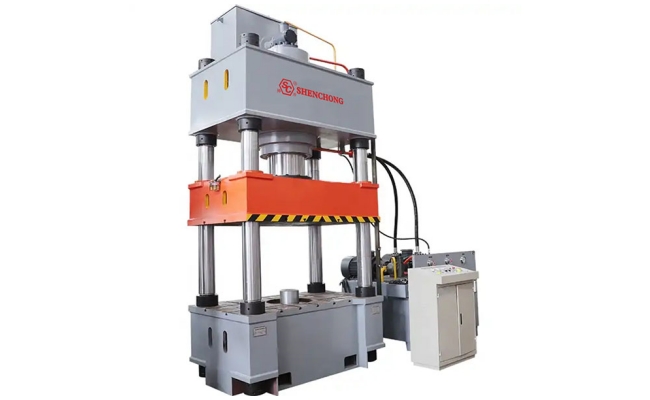
The working priciple of a four column hydraulic press is an oil pump that delivers hydraulic oil to a set of integrated plug valves. Hydraulic oil is distributed to the upper and lower chambers of the cylinder through each check valve and safety valve, and is moved by high-pressure oil. A hydraulic press is a device that utilizes liquid to transmit pressure. When a liquid transfers pressure in a closed container, it follows Pascal’s law.
Four-column Hydraulic Press Working Principle
The hydraulic transmission system of a four column hydraulic press consists of a power mechanism, a control mechanism, an actuator, an auxiliary mechanism, and a working medium. The power mechanism usually uses an oil pump as the power mechanism, which is usually an integrated oil pump. To meet the speed requirements of the actuator, one or more oil pumps can be selected. Low pressure gear pump, oil pressure below 2.5MP, medium pressure blade pump, oil pressure below 6.3MP, high pressure piston pump, oil pressure below 32.0MP. Pressure processing and forming of various plastic materials, such as extrusion, bending, stretching of stainless steel plates, and cold pressing of metal parts. It can also be used to press powder products, grinding wheels, PF resin, and hot resin products.
Four-Column Hydraulic Press Features
Four column hydraulic press machine has an independent power mechanism and electrical system and adopts centralized control of buttons, which can realize three working modes of adjustment, manual and semi-automatic. The machine’s working pressure, pressing speed, no-load fast down and deceleration stroke and range can be adjusted according to the process needs and can complete the ejection process. There can be three ejection processes, such as the ejection process and the stretching process. The process is constant pressure. Two process actions are available for constant pressure. The constant pressure molding process has ejection delay and automatic return after pressing.
Four-Column Hydraulic Press Composition
The four column hydraulic press consists of two parts: the main engine and the control mechanism. The main components of a hydraulic press include hydraulic cylinders, beams, columns, and liquid filling devices. The power mechanism consists of fuel tank, high-pressure pump, control system, engine, pressure valve, steering valve, etc.
Four-Column Hydraulic Press Control
The four-column hydraulic press has an independent power mechanism and electrical system and adopts centralized control of buttons, which can realize three operation modes of adjustment, manual and semi-automatic.
Hydraulic Press vs. Mechanical Press
Power Comparison
Power that each press can produce is a key factor when people compare hydraulic and mechanical presses. Hydraulic presses are known for their high force capacity, capable of applying thousands of tons of pressure. This is because its power comes from the pressure of hydraulic oil, which is easily amplified. On the other hand, mechanical presses generate force through mechanical devices such as gears and levers, which typically have fixed force capabilities depending on their design.
Application Suitability
The suitability of hydraulic and mechanical presses largely depends on specific applications. Hydraulic presses excel in tasks that require high level of force and precision, such as metal forming, composite material forming, and processing. They provide flexibility in terms of control force and can be adjusted according to different materials and thicknesses. Meanwhile, in high-speed production environments, mechanical presses are usually preferred because constant force is required throughout the entire production process. They are usually used for operations such as stamping and forging, where speed and repeatability are key.
Force And Speed Control
In a hydraulic press, you can easily control the force and speed and offer greater flexibility for complex tasks through a control panel. Mechanical presses is difficult to modify a set speed and force. For this reason, mechanical press machine is less adaptable but more straightforward for repetitive tasks.
Safety Features
Considering the volatility of pressurized fluids, most hydraulic presses have built-in safety features. While mechanical presses typically require additional external mechanisms to ensure safe operation.
Understand Hydraulic Press Power
It is crucial to fully tap into the potential of hydraulic presses, especially in industries where precision and power are crucial. Why is this understanding so important? Okay, this is not just about knowing how powerful hydraulic presses are; this is about understanding how to effectively and safely use this power.
First off, safety is a top priority. The immense power of hydraulic presses, capable of exerting thousands of pounds of pressure, also comes with significant risks. Knowledge of a press’s power capabilities helps in establishing safe operating procedures and selecting the right machine for the job. This not only ensures the safety of operators but also extends the lifespan of the machine itself.
Moreover, in the realm of manufacturing and engineering, precision is a game-changer. Understanding the power specifications of a hydraulic press enables you to select the right press for your specific task. Whether it is bending metal, pressing bearings, or molding plastics, the right amount of force is critical. Too little, and the job won not be done; too much, and you risk damaging the material or the machine.
From an economic perspective, efficiency is key of the sheet metal processing. Fully understanding and correctly using hydraulic presses can greatly improve productivity. By optimizing electricity usage, enterprises can save energy costs, reduce mechanical wear, and increase production, all of which contribute to achieving a healthier bottom line.
Hydraulic Press Tonnage Definition
Hydraulic press power, refers to the amount of force exerted by the press ram onto the workpiece. It determines the capacity of the press to deform or shape the material being processed. Tonnage is a critical parameter that directly influences the success and efficiency of manufacturing operations. Hydraulic press ultimate guide teach you how to calculate the hydraulic press tonnage.
In hydraulic presses, tonnage is typically measured in tons (hence the term “tonnage”), where one ton equals 2,000 pounds of force. However, it’s important to note that tonnage does not necessarily equate to the weight of the material being pressed; rather, it signifies the force required to achieve the desired deformation or compression.
Factors Affect Hydraulic Press Tonnage Calculation
There are several factors that affect the power of hydraulic presses. These factors include the efficiency of the hydraulic system, the quality of the hydraulic fluid, and the condition of pressure machine components such as seals and gaskets.
Material Type And Thickness
The type and thickness of the material being worked on significantly influence the required tonnage. Thicker or harder materials require higher tonnage to achieve the desired deformation or shaping.
Different materials exhibit varying degrees of resistance to deformation. Metals, for instance, typically require higher tonnage compared to plastics or rubber. Additionally, the thickness of the material directly impacts the amount of force needed for shaping or forming.
Die Design And Geometry
The design and geometry of the hydraulic press die or tooling also plays a crucial role. Complex shapes or intricate patterns may require higher tonnage to form accurately.
Frictional Forces
Friction between the material and the die surfaces introduces additional resistance, thereby increasing the required tonnage. Higher friction requires increased tonnage to overcome resistance and achieve proper deformation.Proper lubrication and die maintenance can help mitigate frictional losses.
Desired Outcome
The nature of the hydraulic press manufacturing process will affect the tonnage requirements. For example, deep drawing operations typically require higher tonnage than simple bending or punching operations.
Press Configuration
Different types of hydraulic presses (e.g., C-frame, H-frame, four-column) have varying tonnage capabilities and structural limitations. The hydraulic press configuration must be matched to the application’s tonnage requirements.
Calculate Hydraulic Press Tonnage
The formula for calculating tonnage in a hydraulic press is relatively straightforward, involving the area of the workpiece and the desired pressure
Tonnage= (Pressure x Area)/2000
Where:
- Tonnage is the force exerted by the hydraulic press in tons.
- Pressure is the desired pressure applied to the material in pounds per square inch (psi).
- Area is the total contact area between the material and the die surface in square inches.
For example, if the hydraulic cylinder has an area of 100 square inches and the hydraulic pump generates a pressure of 2,500 pounds per square inch, the force generated by the hydraulic press would be:
Force = Area x Pressure
Force = 100 sq. in. x 2,500 psi
Force = 250,000 lbs.
In this example, the hydraulic press would generate a force of 250,000 pounds. This demonstrates the immense power of a hydraulic press.
Choosing The Right Hydraulic Press Tonnage
It is crucial to select the appropriate tonnage for your application to avoid damaging the machine or the workpiece. Choosing too low tonnage may result in incomplete or uneven deformation. Selecting too high tonnage can lead to excessive wear on the press and increased energy consumption.
Hydraulic Press Ultimate Guide - Hydraulic Press Accessories
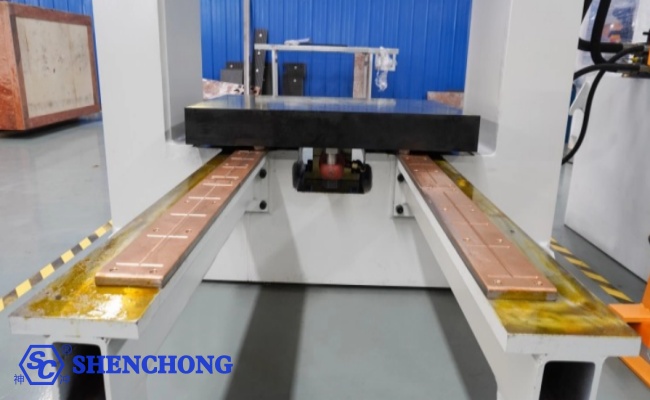
Hydraulic Press Accessories-Die sets
In the context of hydraulic press accessories, “die sets” refer to the tooling components used to shape or form materials. They are often made up of two parts: the upper die (also known as the punch) and the lower die (also known as the die block or die shoe). These components are designed to withstand high pressure and are typically made from hardened steel.
Common Types of Die Sets Used in Hydraulic Press Accessories Include:
- Blank and Pierce Dies: Used for cutting out shapes from sheet metal or other materials.
- Forming Dies: Used for bending, folding, or shaping materials into specific geometries.
- Coining Dies: Used for creating precise and detailed patterns or designs on materials.
- Extrusion Dies: Used for forcing materials through a shaped opening to create long, continuous shapes.
- Drawing Dies: Used for stretching or pulling materials to create cylindrical or tubular shapes.
- Progressive Dies: Used for performing multiple operations on a single workpiece in a sequential manner.
Key features of die sets include robust construction to withstand the high forces exerted during operation, precise alignment to ensure accurate shaping of workpieces and interchangeable components for versatility in production. Advanced die sets may incorporate features such as quick-change capabilities, automated tooling adjustments, and sensors for monitoring and optimizing performance.
Hydraulic Press Accessories-Hydraulic Fluids And Filtration Systems
Hydraulic Fluids
- Hydraulic fluids serve as the lifeblood of hydraulic systems, transmitting power and energy to actuate the press’s various components. These fluids also provide lubrication to minimize friction and wear within the hydraulic system.
- Common types of hydraulic fluids include mineral oils, synthetic oils, water-based fluids, and biodegradable fluids. The selection of hydraulic fluid depends on factors such as operating temperature range, pressure requirements, environmental considerations, and compatibility with system components.
- Hydraulic fluids must exhibit specific characteristics, including proper viscosity, stability, anti-wear properties, corrosion resistance, and compatibility with seals and hoses. Maintaining the correct fluid viscosity is crucial for ensuring efficient hydraulic system operation across a range of operating temperatures.
Filtration Systems
- Filtration systems are integral components of hydraulic presses that remove contaminants, such as particles, water, and air, from the hydraulic fluid to maintain cleanliness and prolong system life.
- Contaminants in hydraulic fluid can cause abrasion, corrosion, and component wear, leading to decreased performance, increased maintenance requirements, and potential system failure.
- Filtration systems typically consist of various components, including filters, filter housings, bypass valves, and differential pressure gauges. Filters may utilize different filtration media, such as cellulose, synthetic fibers, or metal mesh, to capture contaminants of varying sizes.
- Filtration systems may employ different types of filtration, including depth filtration, surface filtration, and magnetic filtration, to effectively remove contaminants from hydraulic fluid.
- Proper maintenance of filtration systems is essential to ensure their effectiveness. This includes regular inspection, replacement of filter elements, monitoring of pressure differentials, and adherence to recommended maintenance schedules.
Hydraulic Press Accessories-Pressure Gauges
Pressure gauges are vital components of hydraulic press accessories, offering essential insights into the force exerted by the hydraulic fluid within the system. Serving as critical instruments for monitoring and controlling operations, these gauges play a pivotal role in ensuring the press functions safely and effectively.
These gauges can be analog or digital, and they display the pressure in units such as pounds per square inch (psi), bars, or pascals.
By observing the pressure readings on these gauges, operators can make adjustments to the press settings as needed to achieve the desired results in terms of force applied, speed of operation, and product quality. They can also use the pressure readings to diagnose any issues or abnormalities in the hydraulic system, such as leaks, blockages, or malfunctions, allowing for prompt maintenance and repairs to prevent downtime and ensure the safe and efficient operation of the hydraulic press.
Hydraulic Press Accessories-Safety guards
Safety guards on hydraulic press accessories are essential components designed to protect operators and other personnel from hazards associated with the operation of the press. These guards serve to prevent accidents, injuries, and potential fatalities by enclosing or covering dangerous parts of the press and controlling access to them.
Hydraulic Press Accessories-Heating And Cooling Systems
Heating and cooling systems on hydraulic press accessories are specialized features designed to control the temperature of the hydraulic fluid and other components of the press. These systems are essential for optimizing manufacturing processes, enhancing product quality, and increasing efficiency.
Heating Systems
- Hydraulic presses may incorporate heating systems to preheat the hydraulic fluid before operation, especially in cold environments or for specific applications requiring precise temperature control. Preheating the hydraulic fluid can enhance its viscosity, ensuring smoother operation and reducing wear on components.
- Electric heaters or heat exchangers are commonly used to heat the hydraulic fluid. These heaters may be integrated into the hydraulic system, either directly within the reservoir or in line with the fluid circulation loop.
- Heating systems can be controlled using temperature sensors and feedback mechanisms to maintain the desired fluid temperature within optimal operating ranges.
Cooling Systems
- Cooling systems are essential for dissipating heat generated during the hydraulic press operation, preventing overheating of hydraulic fluid and hydraulic components. Overheating can lead to reduced efficiency, degraded performance, and potential damage to the press.
- Cooling systems typically involve heat exchangers, chillers, or cooling towers that transfer heat from the hydraulic fluid to a separate cooling medium (e.g., water or air) before recirculating the cooled fluid back into the hydraulic system.
- Temperature sensors and control mechanisms are employed to regulate the cooling process, ensuring that the hydraulic fluid remains within safe temperature limits during operation.
Some advanced hydraulic presses feature integrated temperature control systems that combine heating and cooling functions to maintain precise temperature levels throughout the hydraulic system. These systems may utilize thermostatic control valves, proportional control valves, or electronic control units to adjust heating and cooling rates based on real-time temperature measurements and feedback. Integrated temperature control helps optimize hydraulic press performance, extend component lifespan, and enhance overall system efficiency.
Choose the Suitable Hydraulic Press You Need
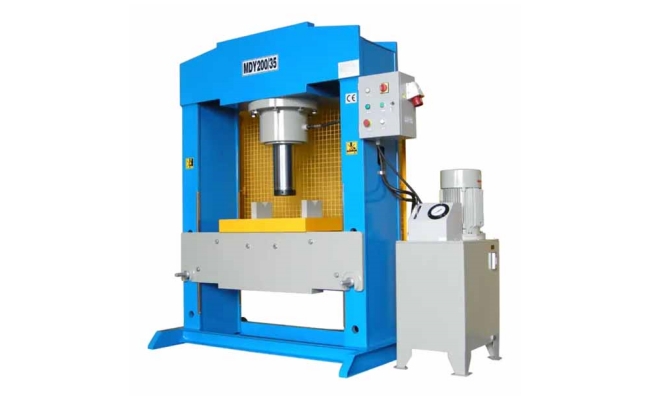
So you’ve learned about the core components, the science, and even the different types of hydraulic presses available on the market. But how do you decide which one is the perfect fit for you? The key to making an informed decision lies in understanding your specific needs and how they align with the features of various hydraulic presses.
Identifying Your Requirements
Before you even start window-shopping, sit down and make a list of your needs. What materials will you be working with? What are the dimensions of your workspace? Do you require a press for professional manufacturing or for smaller projects?
Consulting With A Hydraulic Press Manufacturer
Once you have a clear idea of your requirements, the next step is to consult with a reputable hydraulic press manufacturer. They can provide insights into which machine would be most suitable for your application.
Examining The Specifications
Always check the technical specifications of the hydraulic press. This includes the force capacity, stroke length, and size. These details will help you determine if the press is capable of handling your intended tasks.
Evaluating Additional Features
Many hydraulic presses come with additional features like programmable logic controllers (PLCs), advanced safety features, and customizable worktables. While these may increase the initial cost, they can offer long-term benefits.
Hydraulic Press Maintenance
Hydraulic presses are robust, but they’re not invincible. Like any machinery, they require a regimen of care and attention to operate efficiently over the long term. Knowing how to troubleshoot common issues and conduct preventive maintenance can save you both time and money. Let’s get into the nitty-gritty.
Fundamental Maintenance
- It is recommended to use No. 32 and No. 46 anti-wear hydraulic oil for work, with an oil temperature range of 15-60 degrees Celsius.
- The oil must be strictly filtered before it can be added to the fuel tank.
- The working oil should be replaced once a year, and the first replacement should not exceed three months;
- The slider should be lubricated regularly, and the exposed surface of the column should be kept clean regularly. Before each operation, oil should be sprayed first.
- Under a nominal pressure of 500T, the maximum allowable eccentricity of the concentrated load is 40mm. Excessive eccentricity can easily cause damage to the column or other adverse phenomena.
- Calibrate and inspect the pressure gauge every six months;
- If the machine is not used for a long time, the surfaces of each part should be cleaned and coated with rust proof oil.
After Using Maintenance
The machine tool should undergo secondary maintenance after running for 5000 hours. Mainly consisting of maintenance workers, with operators participating. In addition to performing first level maintenance, the following tasks should be done well and vulnerable parts should be surveyed. Propose spare parts and accessories.
First, cut off the power for maintenance work.
A Crossbeam Column Guide Rail
- Check and adjust the plane of the hanging crossbeam, column guide rail, guide sleeve, slider, and pressure plate to achieve smooth movement and meet the process requirements.
- Repair or replace defective parts.
Hydraulic Lubrication
- Disassemble, clean, and inspect the solenoid valve, grind the valve and valve core.
- Clean and inspect the oil pump cylinder plunger, remove burrs, and replace the oil seal.
- Verify the pressure gauge.
- Repair or replace severely worn parts
- Drive and check that each oil cylinder and plunger runs smoothly without any crawling. The support valve can accurately stop the movable crossbeam in any position, and the pressure drop meets the process requirements.
Electric Maintenance
- Clean the motor, check the bearings, and update the lubricating grease.
- Repair or replace damaged components.
- Electrical appliances meet the requirements of equipment integrity standards.
Machine Precision Maintenance
- Calibrate the level of the machine tool, check and adjust the repair accuracy.
- The accuracy meets the requirements of equipment integrity standards.
The maintenance and upkeep of hydraulic presses still require dedicated, professional, and dedicated personnel to maintain them, so that they can be used for a longer time!
Safety Operation Precautions
- Those who do not understand the structural performance or operating procedures of the machine should not start the machine without authorization;
- During the operation of the machine, maintenance and adjustment of the mold should not be carried out;
- When the machine discovers serious oil leakage or other abnormalities (such as unreliable operation, loud noise, vibration, etc.), it should be stopped to analyze the cause and try to eliminate it. It should not be put into production with problems:
- Do not overload or exceed the maximum eccentricity for use:
- It is strictly prohibited to exceed the maximum stroke of the slider, and the minimum closing height of the mold shall not be less than 600mm.
- The grounding of electrical equipment must be firm and reliable:
- At the end of each day’s work: Place the slider to the lowest position.
Common Faults
During the operation of the metal extrusion hydraulic press, sometimes bolts may fall off and fall into the hydraulic cylinder, causing serious scratches on the plunger wall. After the problem occurs, traditional methods cannot achieve on-site repair at all, and can only be dismantled and transported to the manufacturer for repair welding processing or scrapping and replacement. Due to the lack of spare parts for replacement, it is difficult to control the time required to reproduce or return to the factory for maintenance. Prolonged downtime causes serious economic losses to the enterprise, while also requiring high processing or repair costs. In order to meet the requirements of continuous production for enterprises, it is necessary to find convenient, fast, simple and effective maintenance methods to solve the equipment problem, minimize the downtime of the enterprise, and reduce maintenance costs. Polymer composite materials can be used for on-site repair
Operation Steps
- Use an oxygen acetylene flame to bake the scratched area (control the temperature and avoid surface annealing), and bake out the oil that has been permeating the metal surface for years until there are no sparks splashing.
- Surface treat the scratched area with an angle grinder to a depth of at least 1 millimeter, and grind out grooves along the outer wall of the cylinder, preferably dovetail grooves. Scratches deepen the drilling at both ends, changing the stress situation.
- Clean the surface with a degreased cotton dipped in acetone or anhydrous ethanol.
- Apply evenly mixed repair materials to the scratched surface; The first layer should be thin, evenly and completely covering the scratched surface to ensure the best adhesion between the material and the metal surface. Then, apply the material to the entire repair area and repeatedly press to ensure that the material is filled tightly and reaches the required thickness, slightly higher than the surface of the outer wall of the cylinder.
- It takes 24 hours for the material to fully achieve its various properties at 24 ℃. To save time, the temperature can be increased by a halogen tungsten lamp. For every 11 ℃ increase in temperature, the curing time will be shortened by half. The optimal curing temperature is 70 ℃.
- After the material has solidified, use a fine grinding stone or scraper to repair and level the material that protrudes from the outer wall of the cylinder, and the construction is completed.
Conclusion
Hydraulic press is a machine that uses hydrostatic pressure to process products such as metal, plastic, rubber, wood, powder, etc. It is commonly used in pressing and forming processes, such as forging, stamping, cold extrusion, straightening, bending, flanging, sheet metal drawing, powder metallurgy, pressing, and so on. Hydraulic press ultimate guide introduces all the knowledge you need to know about the hydraulic press machine, including its application, strength and limitation, main parts of the hydraulic press, different types of hydraulic press, hydraulic press tonnage calculation, necessary accessories and maintenance.