One of the press brake application is to bend all kinds of poles, and so press brake factories often receive the clients’ inquiries to produce the press brake for the street light poles and high mast poles bending. Semi-automatic light pole production line is specially designed for poles manufacturing, and below is one of the semi-automatic light pole production line case SC SHENCHONG offered to our client.
Client’s Pole Information
This client has two types of poles want to produce: one is the polygonal poles and another is conical poles.
Polygonal poles (Material: S235) | maximum number of strokes | 16 |
|
max dimensions |
|
|
|
| thickness | 6 | mm |
| length | 12000 | mm |
| diameter (single piece) (minimum) | 160 | mm |
| diameter (single piece) (maximum) | 500 | mm |
Conical poles (Material:S235) |
|
|
|
max dimensions |
|
|
|
| thickness | 4 | mm |
| length | 12000 | mm |
| diameter (single piece) (minimum) | 60 | mm |
| diameter (single piece) (maximum) | 210 | mm |
| conicity/cone reduction a long the length |
|
|
|
|
|
|
min dimensions |
|
|
|
| thickness | 4 | mm |
| length | 6000 | mm |
| diameter (single piece) (minimum) | 60 | mm |
| diameter (single piece) (maximum) | 135 | mm |
| conicity/cone reduction a long the length |
|
Light Pole Manufacturing Technology Process
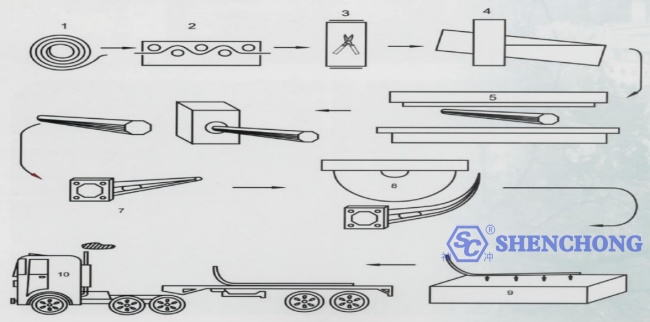
Semi-Automatic Light Pole Production Line Process Flow
- Uncoiling
- Plate leveling
- Plate cutting
- Plate oblique shearing machine
- Leveling the slitting sheet plate again to reduce the stress.
- Stacking of longitudinally cut boards on the unloading device (the process from decoil to stacking the sheet is automatic).
- Use crane to transport stacked sheet to the press brake.
- Double beam truss loading system to loading the sheet to the press brake front feeding device.
- Bending lighting pole
- Pole jointing welding machine(tandem press brake unloading poles connect with welding machine).
Main Production Equipment
- Decoiling – levelling – cutting line
- Slitting Machine
- Double beam truss loading system
- Tandem press brake
- Pole Jointing and welding machine
CNC Cut To Length Line For Light Pole
Model: CTLA6x1600
Automatic type,With four lay type leveling machine+ shearing + 3 blades edge slitting + taper slitting unit.

Features
- The raw material is steel coil, and the output is isosceles trapezoidal plate suitable for the size of street light pole
- Uncoiling, leveling, length cutting, edge removal, oblique shearing, unlading and stacking in one production line. It is a machine and a process. After the plate shears cross cut, there is no need to drive the crane for loading and unloading, and directly enter the oblique shear process. Reduce the number of operators, labor and improve the production speed.
- Full automatic type, sheet length CNC control, sheet quantity CNC control, automatic oblique shear, automatic unloading and automatic stacking system.
- The production speed is extremely fast, because the speed is far faster than the subsequent process. Generally, after this process is completed, the operators can work in other processes, which greatly saves working time and reduces production costs.
- The operator shall be relaxed and minimize contact with the steel plate, which is safe for personnel.
- The shearing machine has the function of overall rotation, which can rotate at a certain angle relative to the center line, so that the cut plate is parallelogram, which is convenient for the oblique shearing machine to obtain isosceles trapezoid plate after oblique shearing, which is suitable for the production of light pole. There is no need for trimming process to reduce sheet metal waste.
- Three blade edge cutting device, which can remove the waste edge and cut the middle half at the same time when the sheet width can be used as four poles.
- After oblique shearing, the plates in the same direction are stacked separately without sorting. Multiple plates (such as 30 plates) can be directly hoisted to the bending machine, which is safe and saves time.
- The optional leveling unit after taper slitting , which can remove the stress caused by the taper cutting and make high-quality light poles.
Technical Parameter And Composed Devices
Technical Parameter
- Thickness of material: hot rolled mild steel Max:6mm, Min: 2mm for Q235,Q345, yield strength: 235Mpa, 345Mpa
- Max width of steel plate: 1600mm
- Weight of steel coil: Max 30 tons
- Inner diameter of steel coil: Φ508mm- Φ760mm
- Leveling speed: 5- 15m/min
- Number of leveling rollers:13, up roller 6, bottom roller 7
- Leveling rollers diameter: 132mm
- Leveling roller distance: 143mm
- Leveling roller material: GCr15
- Leveling roller hardness: HRC55-58
- Supporing roller device: up and low rollers each 3 units
- Supporting roller diameter: 140mm
- Length range for scale: 2000~12000mm according requirements
- Tolerance of cutting length: less ±2mm (base on 8m length plate)
- Main leveling motor power: 37kw, 960RPM
- Shearing machine capacity: 6mmx2500mm
- Shearing machine rotation angle: 1.5 degree.
- double edge and taper Slitting speed: 15 m/min.
- Power of the main motor for slitting: 5.5kw
- Dolly moving speed: 15m/min. adjustable
- Slitting blade material: H13k
- Slitting blade diameter: 280mm
- taper slitting Pinching roll diameter: 280mm
- inner Width of edge slitting unit: 1550mm
- inner Width of taper slitting unit: 1800mm
- width area for machine: about 7200mm
Detail Of The Device
- Steel coil loading dolly car
- Hydraulic double-head umbrella type decoiler
- Hydraulic pressing and guiding, hydraulic shovel-head device, pinching device
- Middle rolling way worktable
- Guiding device
- Leveling unit: (four lay type)
- Rotating typeShearing machine
- Pole length supporting table + trolly ,with Automation device :
- Plate rising device.
- Three blades edge slitting unit.
- Pole length supporting table + trolly with Automation device
- Plate rising device.
- Taper slitting unit
- Ball type support table for unloading
- Taper plate unloading and stacking automatic system
- Electrical system
- Hydraulic system
- Pneumatic system
Option Items
Option 1: Leveling Unit after taper slitting,
Option 2: Plate offline system
Option 3: Remote diagnosis function.
Option 4 Spare parts
Double Beam Truss Loading System
After slitting and leveling, using a crane to manually lift a stack of sliced boards to the truss station in front of the bending machine.
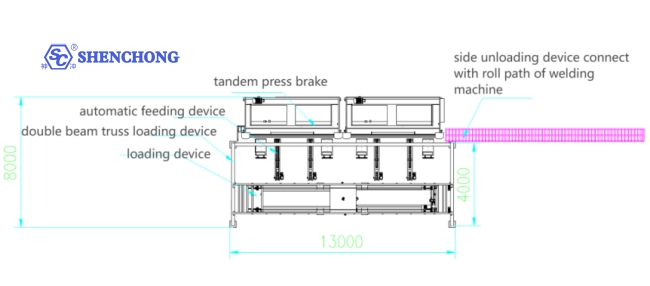
Workflow:
Vacuum sucker cup of double beam truss loading system grab the plate from the slitting machine roll path.
Load the plate on the automatic front feeding device of the tandem press brake.
Automatic front feeding device of press brake feeds the plate.
Tandem press brake bend the workpiece.
After bending, CNC controlled side unloading device to unload the finished poles.
Finished poles are loading on the roll path of welding machine.
- Double beam truss loading system include 2 workstation, each workstation is 2000mm long, and so the double beam truss loading system is 4000mm long.
- Double beam truss loading system load weight Max. 1200kg, adopt gear and rack, linear guide as transmission device. Loading part uses servo drive and vacuum sucker cup.
CNC Tandem Press Brake
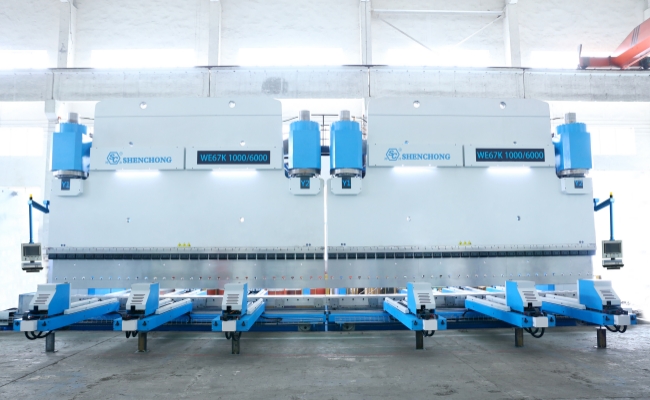
To meet the client bending requirements, we recommend tandem CNC press brake model: 2-WE67K 600 Tons 6000MM, which total is 1200Tons 12000mm. This machine we design for light poles, material , max. thickness 6mm, Max.length 12000mm, pole diameter 60-500mm.
Special Design For CNC Tandem Press Brake In Semi-Automatic Light Pole Production Line
- Automatic front feeding device controlled by CNC
- Automatic back feeding device controlled by CNC system
- Automatically side unloading device
- Automatically suck(including magnetic separation structure, automatically loading structure.
Machine Parameter
Model | 2-WEK-600/6000(ESA-S860) | ||
No. | Item | Unit | value |
1. | pressure | KN | 2×6000 |
2. | Working table | mm | 2×6000 |
3. | Distance between housing | mm | 4800 |
4. | Throat depth | mm | 1250 |
5. | Ram stroke | mm | 300 |
6. | Approaching speed | mm/s | 100 |
7. | Working speed | mm/s | 8-12 |
8. | Return speed | mm/s | 60-100 |
9. | Axis(13+2) |
| Y1,Y2,X1,X2,X3,X4+V1 Y3,Y4,X5,X6,X7,X8,C+V2 |
10. | Y1,Y2,Y3,Y4 parallel tolerance | mm | ±0.01 |
11. | Front feeding stroke | mm | 1800 |
12. | Rear feeding stroke | mm | 1250 |
13. | Daylight | mm | 980 |
14. | Main motor | kw | 37×2 |
15. | Single Machine Overall Dimension (LxWxH) | mm | 6600*3700*4700 |
16. | Single Machine Weight | Ton | 56 |
CNC axis specification:
Y1,Y2,Y3,Y4 axis–control cylinder axis, X1,X2,X3,X4,X5,X6,X7,X8 axis –control feeding axis, C–control side unloading axis, V1,V2–cnc control table crowning
Main Performance And Characteristics
- The frame consists of fuel tank, tray, support, work table, left and right wall panels and sliders. The structure, high structural strength and large steel degree ensure the structural strength of the frame and adopt vibration to eliminate stress.
- The structural parts are rusted by shot blasting and sprayed with anti-rust paint.
- Wall panel, slider and workbench are processed by one-time large-scale CNC floor boring and milling machine to ensure the parallelism and verticality of each mounting surface.
- The principle of machine synchronization: the application of electro-hydraulic servo proportional valve to ensure synchronization of the two machines, the use of the German company’s electro-hydraulic servo proportional valve, its performance characteristics are high-operating force continuous action of the electromagnet, the friction of the mechanical movement pair A small precision electronic amplifier with fast operating characteristics. A grid is installed at each end of the vertical plate of the workbench, which continuously reflects the stroke position and synchronization error of the slider and sends the two differences into the microcomputer control system to control the electro-hydraulic servo proportional valve to synchronize the twin-cylinders of each single machine. Since the grating scale is not directly mounted on the frame wall panel, but is mounted on a C-shaped frame fixed to the table vertical plate, and the work table is used as a reference point, the slider itself and the frame are under load. The deformation does not affect the measurement and control accuracy of the scale. The two-machine synchronization of the two-machine linkage transmits the mechanical synchronization information into an electric signal to the synchronizing board and the microcomputer through a differential potentiometer installed between the two sliders, and controls the electro-hydraulic servo proportional valve through the amplifying board to make the dual-machine Synchronous action.
- The operator can directly perform man-machine dialogue through the computer, displaying in Chinese and English, automatically calculating and adjusting the bending force, optimizing the bending sequence, calculating the length of the workpiece, showing the shape and necessary operation information before and after the workpiece is processed, and Automatic calculation control top dead center, speed change point, image display, full-featured, with programming, jog, pressure, slow recovery control and other functions.
Hydraulic System
- It is driven by electro-hydraulic servo valve group imported by German company. It has compact structure, strong sealing performance, high synchronization precision and long service life.
- External large-diameter filling valve with high speed and low loss.
- Using Sumitomo internal gear high pressure pump can withstand high pressure and low noise.
- The cylinder seal adopts the sealing component of Sweden SKF Company, which has low wear and no leakage.
- The hydraulic system has overload overflow safety protection.
- The cylinder is integrally forged with 45 steel. After rough machining, heat treatment, finishing and fine grinding, the inner wall of the cylinder has both hardness and wear resistance, and high cylindricity precision.
- The plunger is integrally forged by 45 steel. After rough machining, heat treatment and fine grinding, the surface is coated with nickel and phosphorus by the most advanced military technology in the country. The cylinder plunger has good self-lubricating property and can greatly improve the service life.
- The oil level has a clear and intuitive display.
- High-precision guiding system, position measuring system and hydraulic balancing function can meet the needs of full-length machining.
- The equipment can work continuously for 16 hours under the rated load, while the hydraulic system has no leakage and the work is stable and the performance is good. The oil temperature can be controlled within the national standard (≤60~70°C).
Electrical Control System
- The electrical components comply with international standards, are safe and reliable, have strong anti-interference ability, and the electric control cabinet has heat dissipation function.
- It has a movable foot switch for easy operation and an emergency stop function.
The Machine's Anti-Offset Ability
The electro-hydraulic servo system of the machine is a position control system, which dynamically detects the synchronization error of the slider through the grating ruler, and corrects the synchronization error of the slider by the electro-hydraulic servo valve signal given by the numerical control system, so that the slider is completely In the case of partial load, it can always be parallel to the table.
CNC POLE SHUT- WELDING MACHINE
MODEL: HM500/12000
Scope of application: suitable for large length medium size pole longitudinal automatic closing welding, like 5G pole, monopole, highmast pole and normal street light pole.
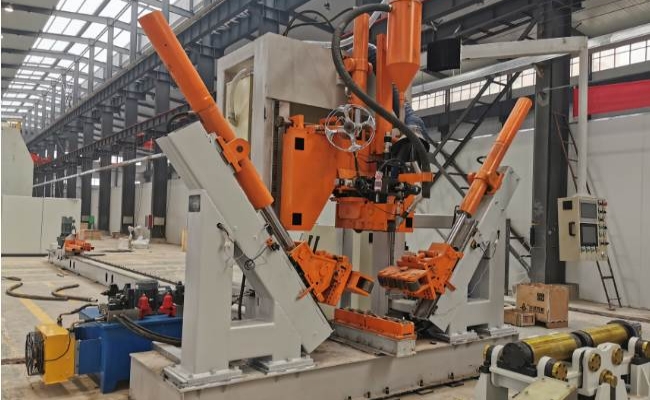
Features
- CNC automatic adjustment, CNC system, with the change of pole diameter, automatically adjust the pressure, automatically adjust the presser foot position, automatically match the feeding speed and position, keep the welding seam always in the closed state, to ensure the smooth welding.
- On the basis of the qualification of the previous process, after welding, there is no torsion of the pole weld, and there is no need for personnel to pry and twist the rod at the back of the machine to center the weld.
- The driving pole is controlled by frequency conversion, with electric brake stop function to ensure the stability of head and tail welding,this system can weld the pole from small end to bottom end full area and almost no left length out of welding. This way is reduced the manual working of the next process.
- The number of clamping roller is 3 sets, the advantage is reduce the roller pressure to the pole surface , and reduce the scratch on the surface . It is suitable for the production of octagonal pole, polygonal pole and conical pole. It can be equal diameter or conical.
- The pushing type trolley with motorized fast returning back function, no need operator to push back manually and it reduces the labor intensity of operators.
- The rear push trolly with pneumatic clamping device, It’s simple and fast compared with manual clamping.
- Submerged arc welding function
- The unloading side is roller type, which is convenient for loading and unloading, and is conducive to realize the automation of upstream and downstream materials. The loading and unloading can be on same side to make operator avoid the long-distance movement. The operator only need to work in the position of the host machine, which greatly reduces the labor intensity.
- The self-developed oil pressure and control synchronization system reduces the requirements for the pole, making the pole after welding more rounded and less deformed.
- Operator: 1 person.
- Unloading roller rack,5 sets(suitable for 12,14m pole)
- According to the layout of the buyer’s workshop, machines with different working directions can be provided
- For the special requirements of customers, machine can be specially designed and manufactured to meet different poles all over the world
- Through the camera installed on the machine head, the welding seam is reflected on the screen of main control panel, making the tracking of the welding seam simple and easy, and reducing the labor intensity of the operator for monitoring of the welding.
The Machine Consists Of The Following Parts
- Long worktable for trolley moving
- Main gantry frame
- Trolley drive system
- Unloading roller rack,5 sets(suitable for 12,14m pole)
- Hydraulic clamping part(Including clamping rollers, suitable for medium size pole)
- Submerged arc welding system, with wire feeding system
- Flux recovery system
- Hydraulic system
- Control system
- Camera, welding seam monitoring system. Clamping roller, in accordance with customer’s pole requirements. With 1 set suitable for monopole High mast, 5G pole mold. with
- 1 set suitable for normal street light poles, minimum diameter of 60mm (round poles and conical pole)
- 1 set suitable for normal street light poles, minimum diameter of 60mm (octagonal pole)
- A set of rear clamping devices suitable for normal street light poles . (Includes a small tool, suitable for poles with very short length, such as 1~2 meters long arm)
- Street light pole loading and unloading system (optional)
- Networked production data system
- Remote diagnosis function
- Oneyear spare parts
Semi-Automatic Light Pole Production Line Production Efficiency
By adopting above semi-automatic light pole production line for 12000mm poles, the client achieves excellent production efficiency result.
- Cut to length line + slitting machine for normal street pole manufacturing: 200~250 pieces/ 8hours.
- Press brake: normal street pole and high mast pole: 80-160 pieces/ 8hours.
- Shut pole welding machine: normal street pole : about 50 pieces/8 hours.
Conclusion
Semi-automatic light pole production line includes slitting machine, cut to length line, plate shearing machine, automatic loading machine, tandem press brake, frame welding machine. Different factory layout and different poles manufacturing requirement should use different production line proposal. Welcome to contact with us for more light pole production line proposals.
Related Article: